Millions of collisions at 300 km/h - Ouch!
Rotor blades are made of strong materials that look indestructible, yet they get damaged by water and that costs a lot of money. Harald van der Mijle Meijer (TNO), and Julie Teuwen (TU Delft), put on their rainboots to research how rain impacts the wind turbines’ rotor blades. The goal? To get more insight into how the damage of blades evolves and even better: how to prevent it.
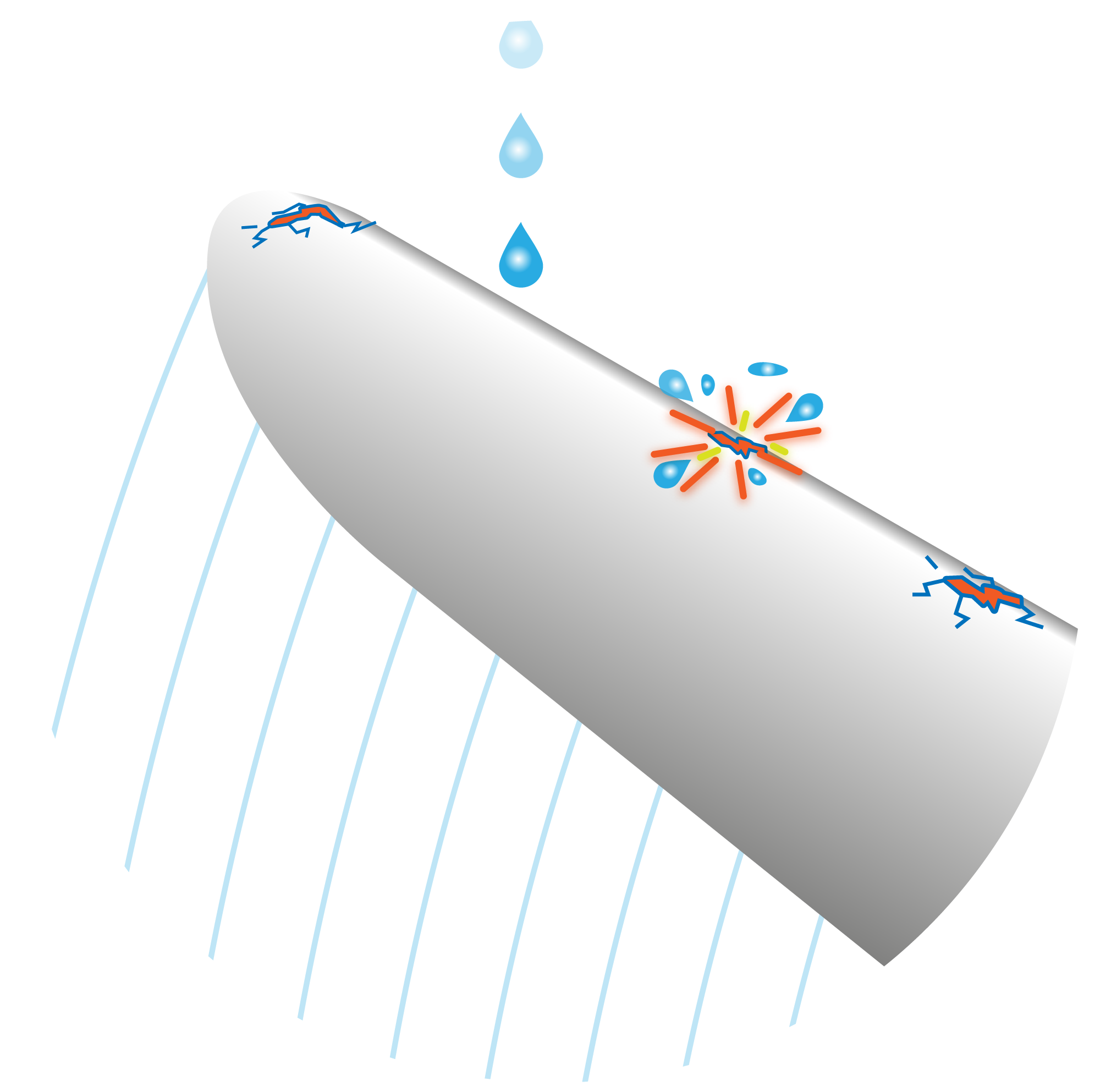
Damaged blades produce less electricity
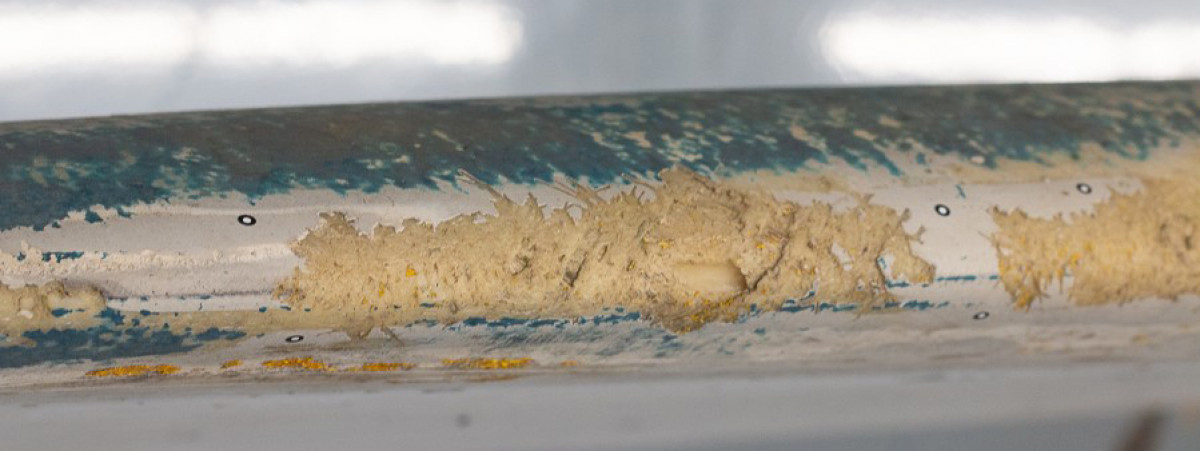
Formation of damage
Sure, you might think it’s just water, and hardly impactful. But it is. Harald: "The rain droplets hit the rotor blades at a relative speed of over 300 km per hour and they almost completely pass over their energy to the blade. Again and again. That hurts.” The damages caused by this are costly and time-consuming to repair. And they also decrease the energy yield. Reason enough to find solutions to prevent the current situation for wind farm owners.
We can prevent damage
With the analysis of lots of data in TNO models the project found some sort of optimum, in which the tip speed is reduced during heavy weather conditions to prolong the lifetime of the blade, and still produce an acceptable amount of electricity.
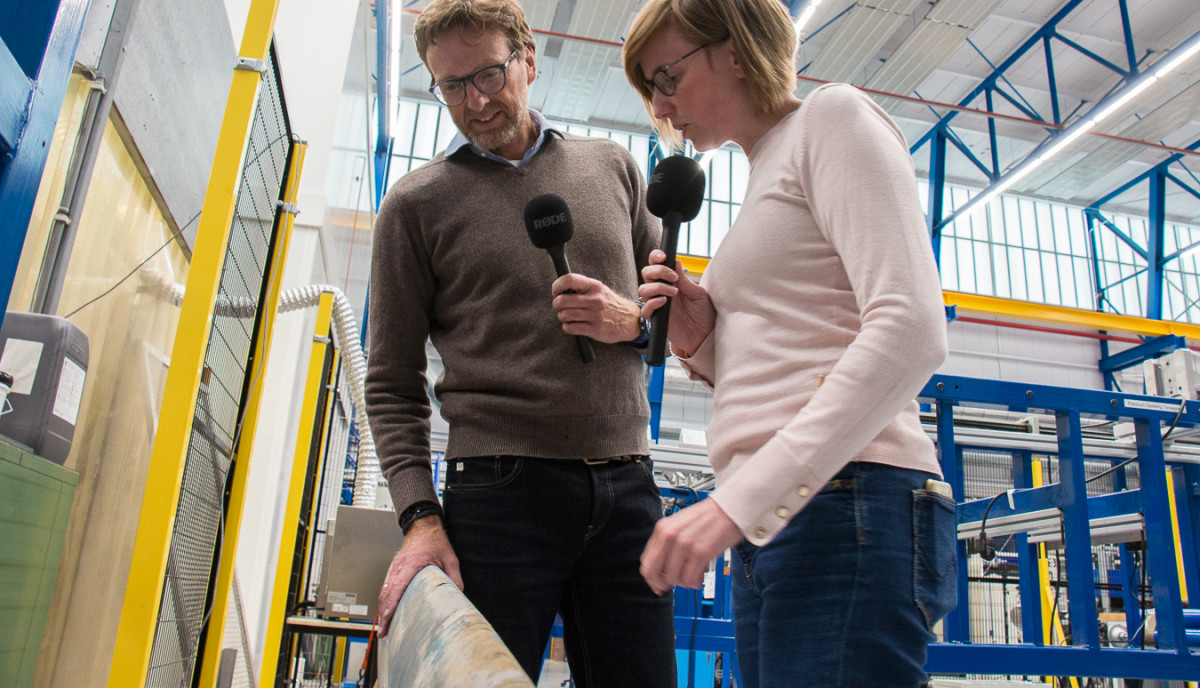
Missing data
However, the project was not without challenges. Harald elaborates: “At the beginning, we found out that the data on precipitation was lacking. We needed to get data on the distribution and the size of the droplets, however, that information hadn’t yet been measured. We used the disdrometer data of KNMI site in De Bilt and extrapolated this to offshore conditions.
The rain-making machine
A big pump provides so much pressure that water is pushed through tubes at a speed of usually 130-170 metres per second. A disk quickly rotates to “cut” the water, so that the water stream is turned into water droplets. These droplets are shot at a rotor blade sample. This way, the harsh weather conditions of rain and wind that rotor blades are subject to are recreated, so that erosion can be purposely caused - and so that it can be studied.
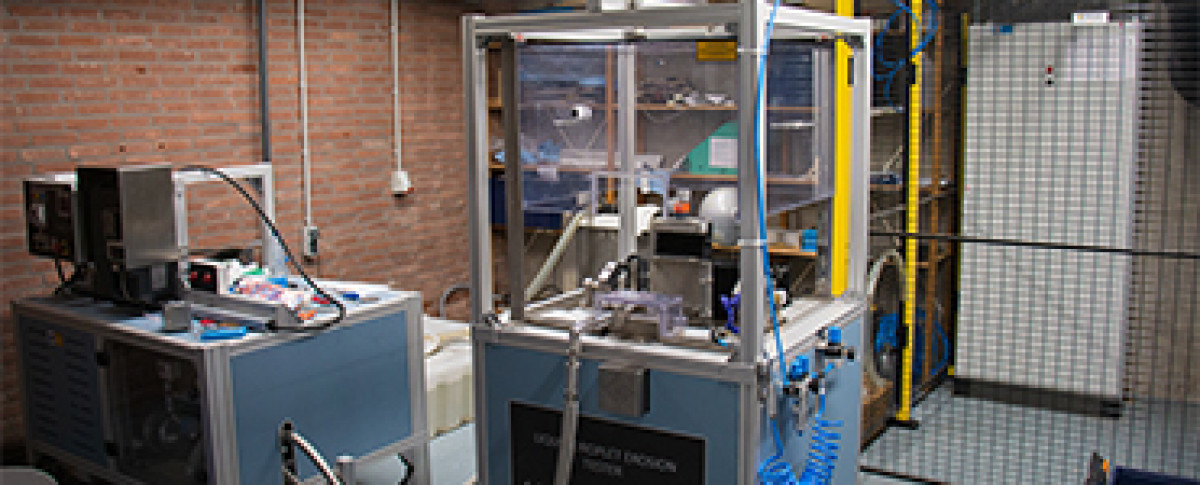
According to Julie, the “idea behind the rain machine is that we can test different coating materials in a laboratory setting, so that we can control all the relevant parameters. Then, we can get a better understanding of the mechanisms behind erosion. With that understanding, we can develop new coating materials or provide pointers to the coating manufacturers.”
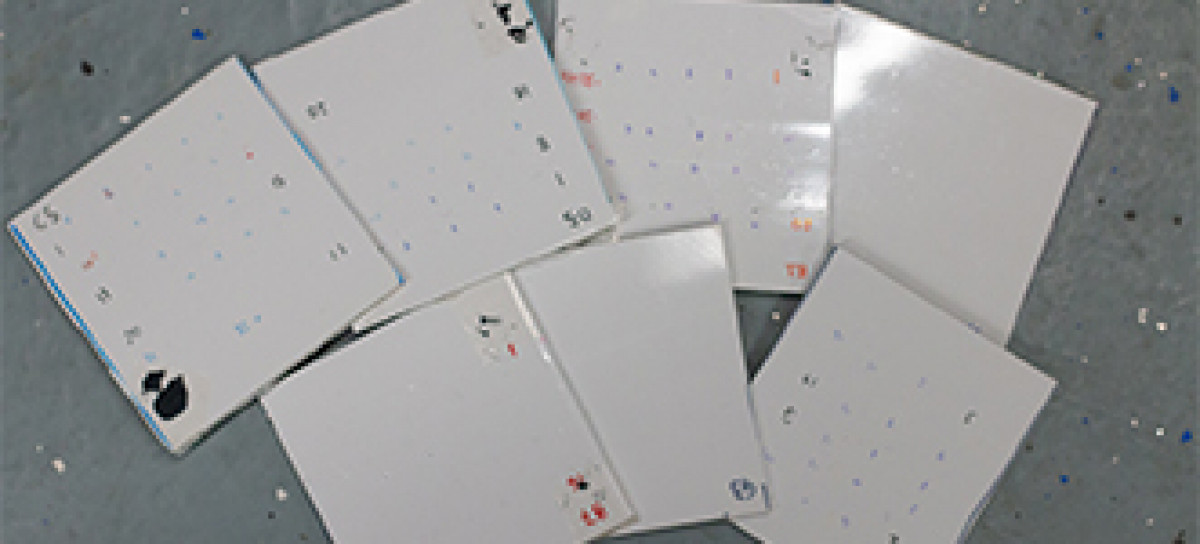
Other than the coating material, the complex mechanisms of erosion are also being tested. How is damage initiated? How does damage progress? What are the performance losses? Answers to all these questions - and more - will help identify the incubation time. More importantly, it will help to find out how the incubation time can be prolonged as much as possible. Knowledge of this will help to potentially prolong the lifetime of rotor blades, and lower maintenance costs and efforts.
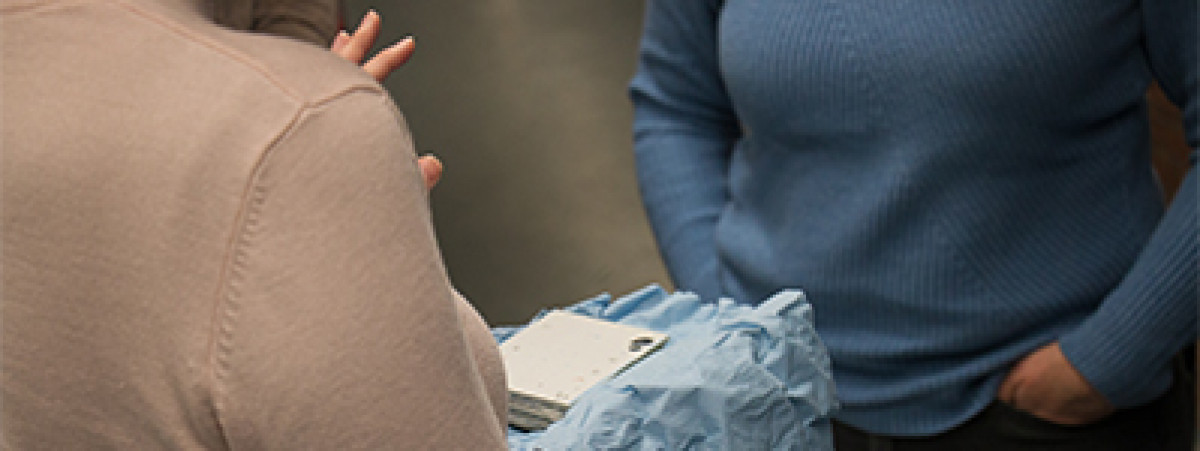
Combining knowledge of different disciplines
Of course, such a challenging and multidisciplinary project cannot be brought to a successful end without several partners. The open data from the KNMI was instrumental to understand the rain and wind conditions at several locations in the Netherlands. Industry partners, such as RWE and Shell – as operators of wind farms the main “problem owners” - are also involved to help solve the problem. And RWE ensured that relevant coating systems were tested in the project. Wind turbine manufacturer Suzlon has shared the designs of their blades and made the panels which were then coated and tested in the project. In a follow-up project, even more parties will be included, such as meteorological partners, operators, and research institutes.
Harald enthusiastically highlights that “we are proud of what we added to the research community on this topic”. As a result, the insights will not stay secret. Reports and articles have already been published to share what has been found so far.
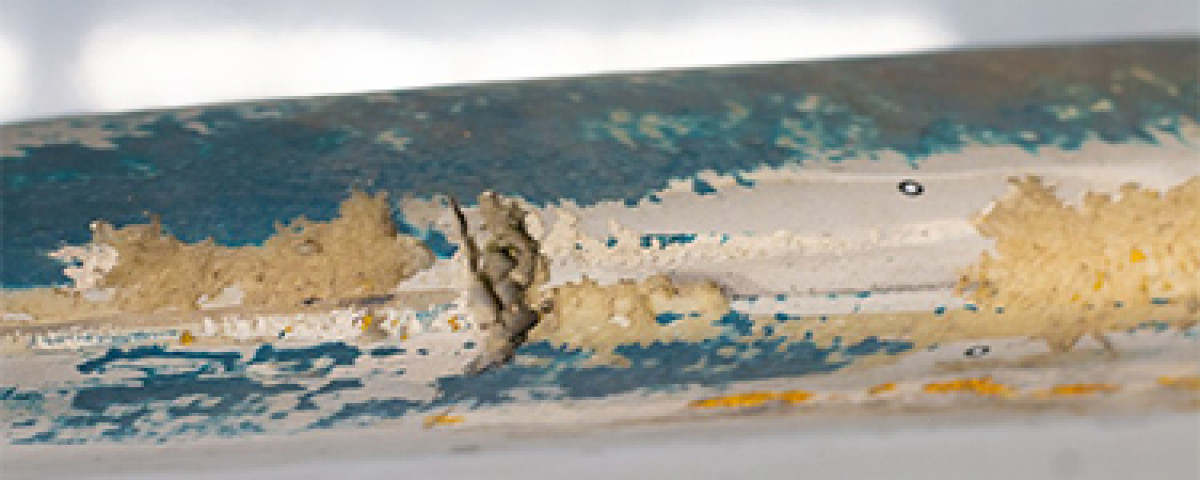
A maintenance-free blade
Finally, Julie shares Harald’s belief that “it is possible to end up with a maintenance-free blade”. Such a blade would not only significantly lower maintenance efforts and costs but also suspend the possible energy loss. This could easily save for the owner of an offshore wind farm of 770 MW approximately a million euros each year, if not more. This decrease in costs is so significant.
Find out more about the WINDCORE project
© GROW ’25