Under Pressure
At the end of a wind farm’s lifetime, everything has to be removed. Current practice is to cut the monopiles that support the wind turbines several meters below the seabed. In the second Hydraulic Pile Extraction Scale Tests (HyPE-ST 1.2) project, Anderson Peccin da Silva and Alba Rodríguez Piedrabuena, both from Deltares, are investigating a new hydraulic pile extraction technology. In this edition, they tell us more about this promising decommissioning technology.
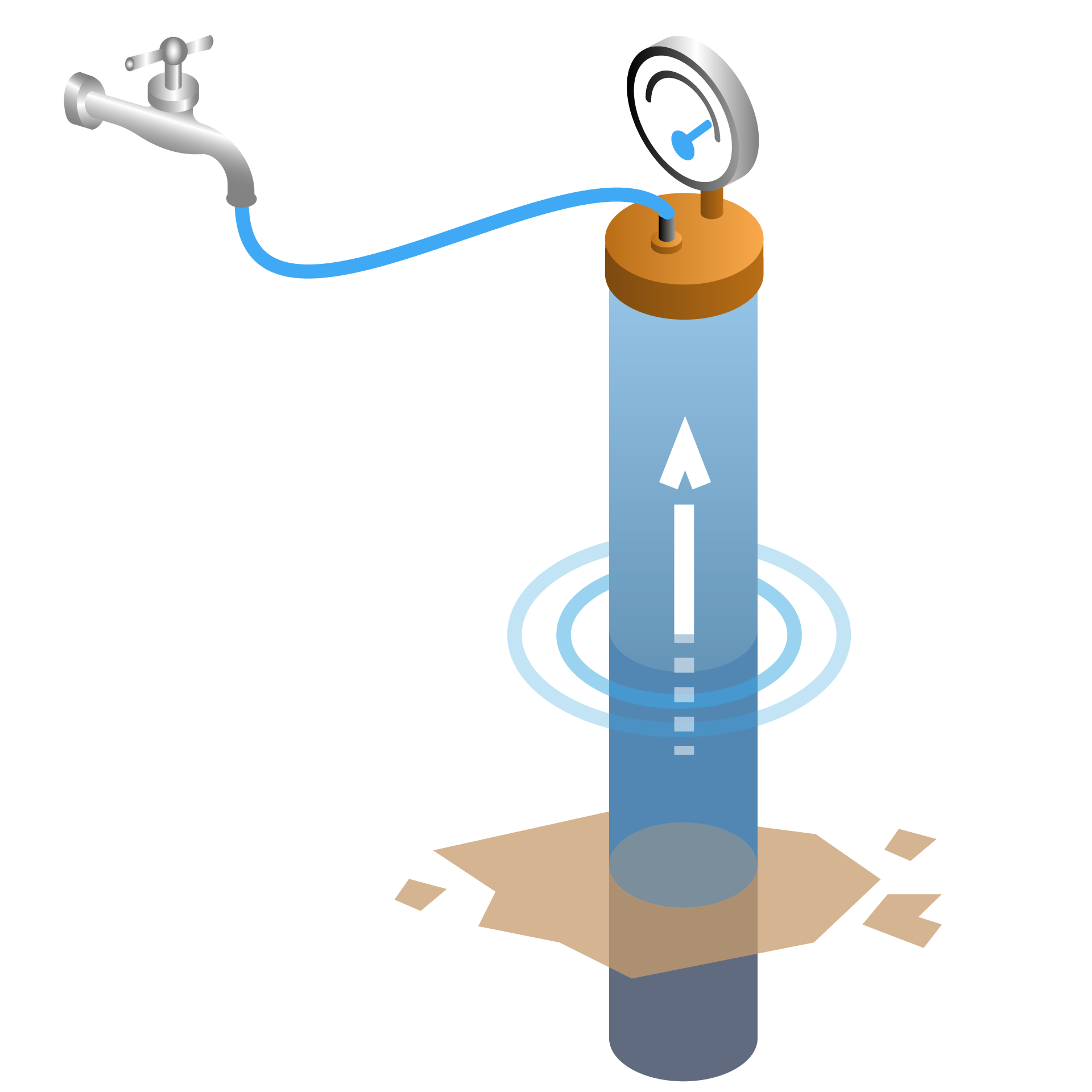
Saving monopiles
But like always, the most important question is: It sounds nice, but how do we do that? Anderson answers: “The monopile sticks out above the water level. We can seal the top of the monopile with a lid and a gasket to ensure that no water leaks out. A valve in this lid is then connected to a pump which injects water into the pile.” And then the magic happens.
Have a look at Anderson's profile on LinkedIn.
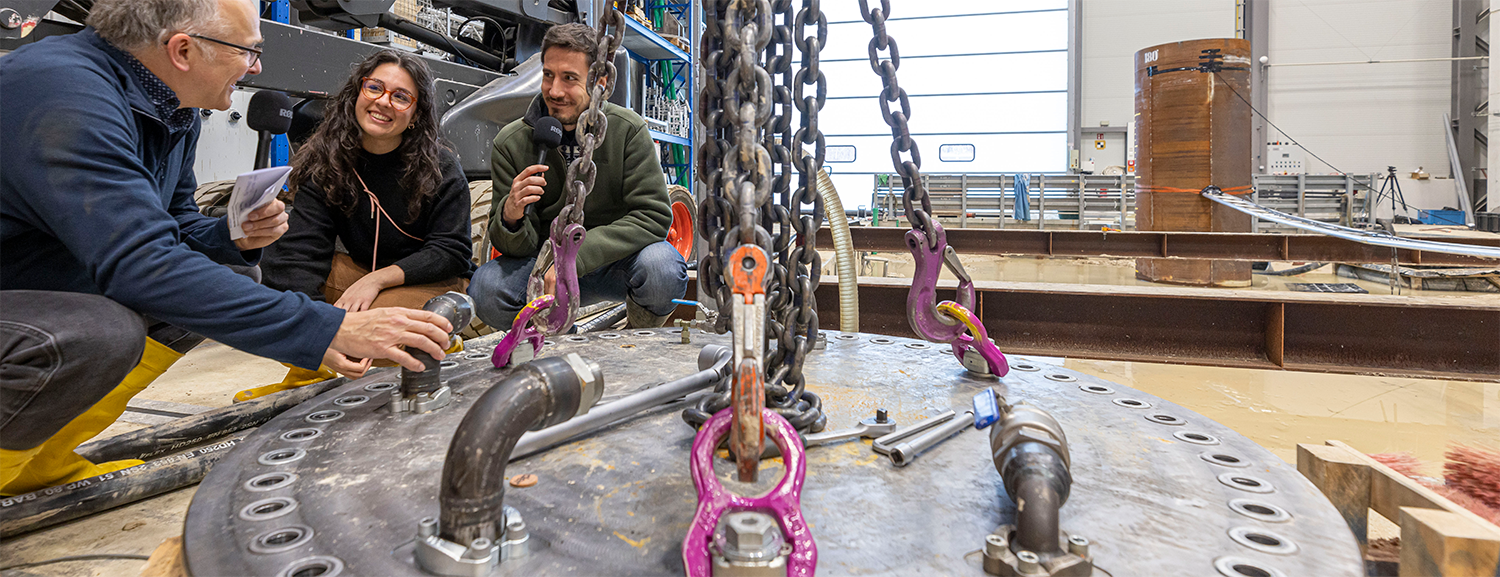
Popping the cork
Have a look at Alba's profile on LinkedIn.
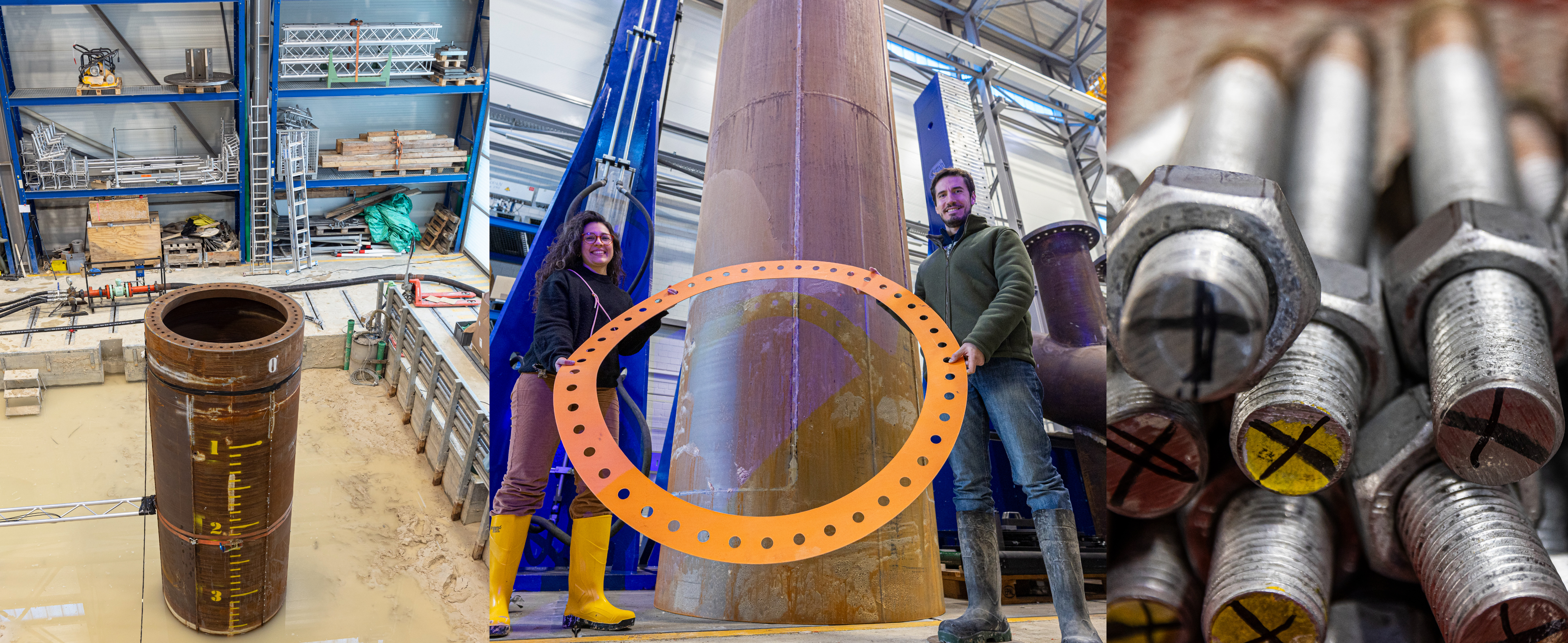
Start small, dream big, bigger, biggest
Of course, the experiment started with models, calculations, and ideas. Anderson: “In HyPE-ST 1 project, together with TNO and Jan De Nul, we developed a numerical model to predict the breakout pressure. That is the pressure required to extract the pile, basically, and Alba very accurately calculated the pressure,” says Anderson. Anderson and Alba do not want to spill more secrets about this pressure point. However, we know that it is “very high” compared to pressures we are used to on daily life such as a car tire.
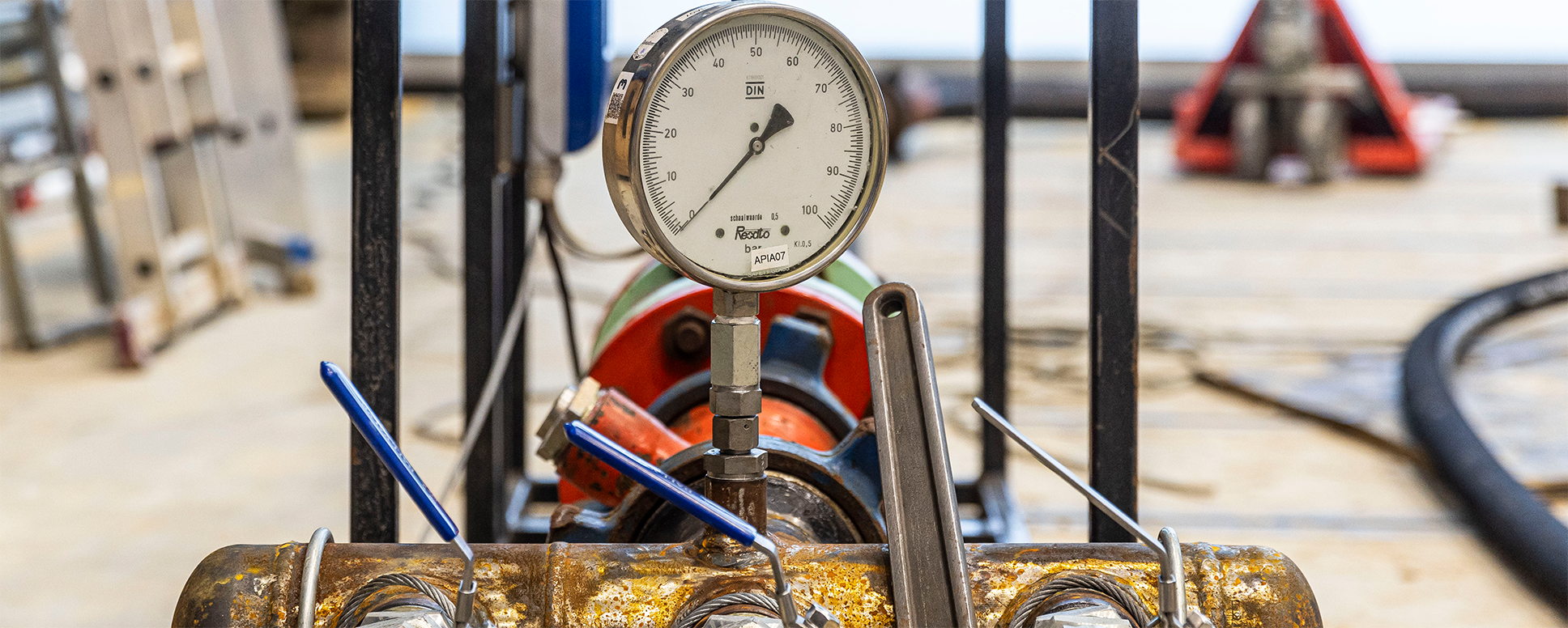
Alba explains why the team ended up at the Testzentrum Tragstrukturen in Hannover: “The Deltares facility in the Netherlands was simply too small for the experiments we wanted to do! This test hall has a deeper basin (10 metres), and the roof here is high enough to be able to install the pile.”
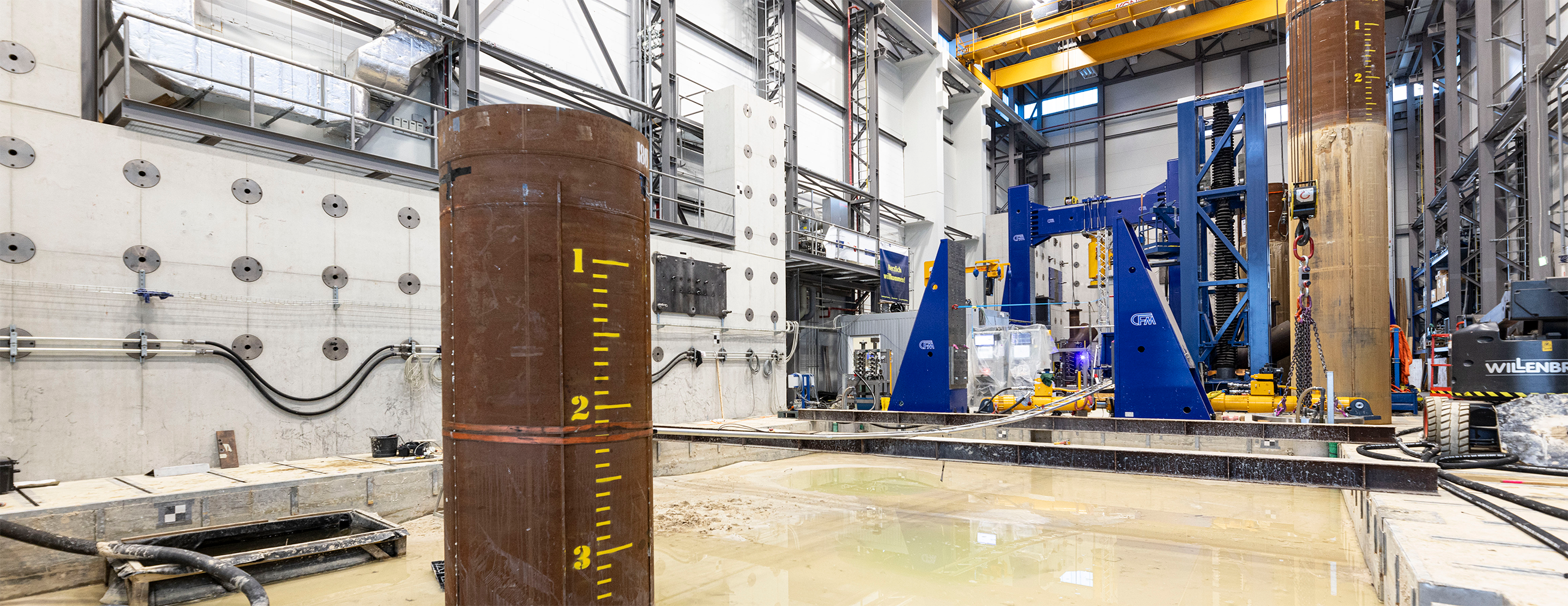
Anderson: “There was still an uncertainty about the scale. The model was validated through small-scale tests; however, there is always uncertainty when you scale things up. Fortunately, we proved that the principle works and that the model is sufficiently accurate.” The extraction of the first pile was celebrated like a goal in football. “Of course, we still have to analyse the data in more depth. But so far it is looking very good.”
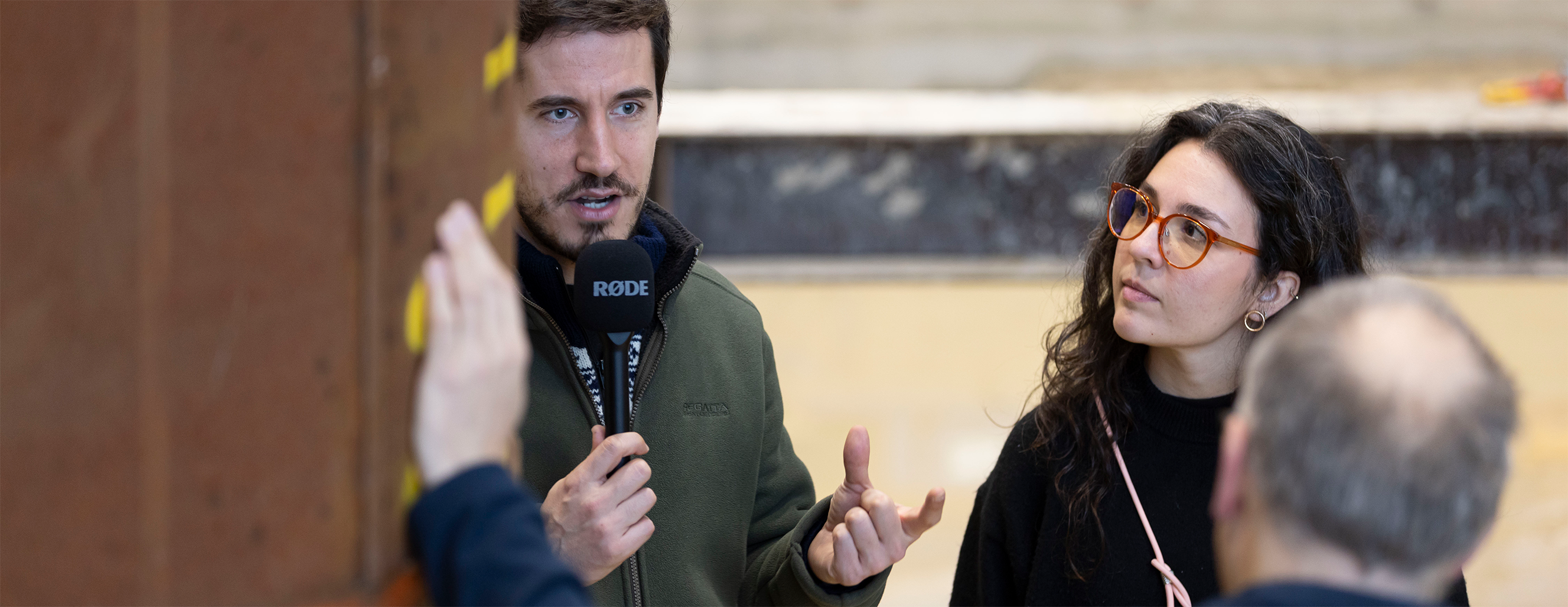
“The monopiles in this experiment have a diameter of about one and a half metres. And still the scale is 1 to 5. So in reality, the actual monopiles offshore are five times larger than the ones we are testing here. Still, this scale is large enough to have representative results.”
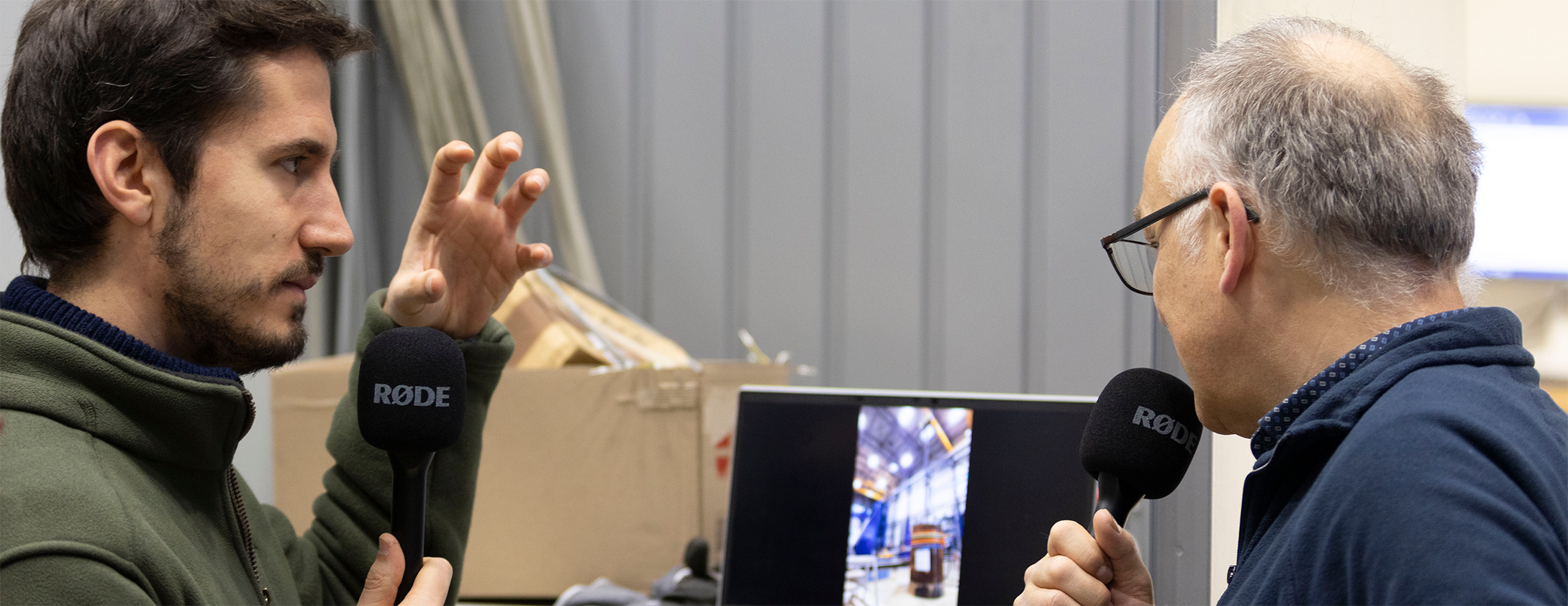
Pressure on the pile… and the project
Despite successful tests, there was also some stress: “There was a moment of tension when we received the CPT results and we saw that the soil in the test basin was slightly denser than we expected. Because the denser the soil, the more difficult it is to hammer the pile in, and the greater the friction between the soil and the pile, the larger the pressures must be to extract the pile. Thankfully, the tests went great.
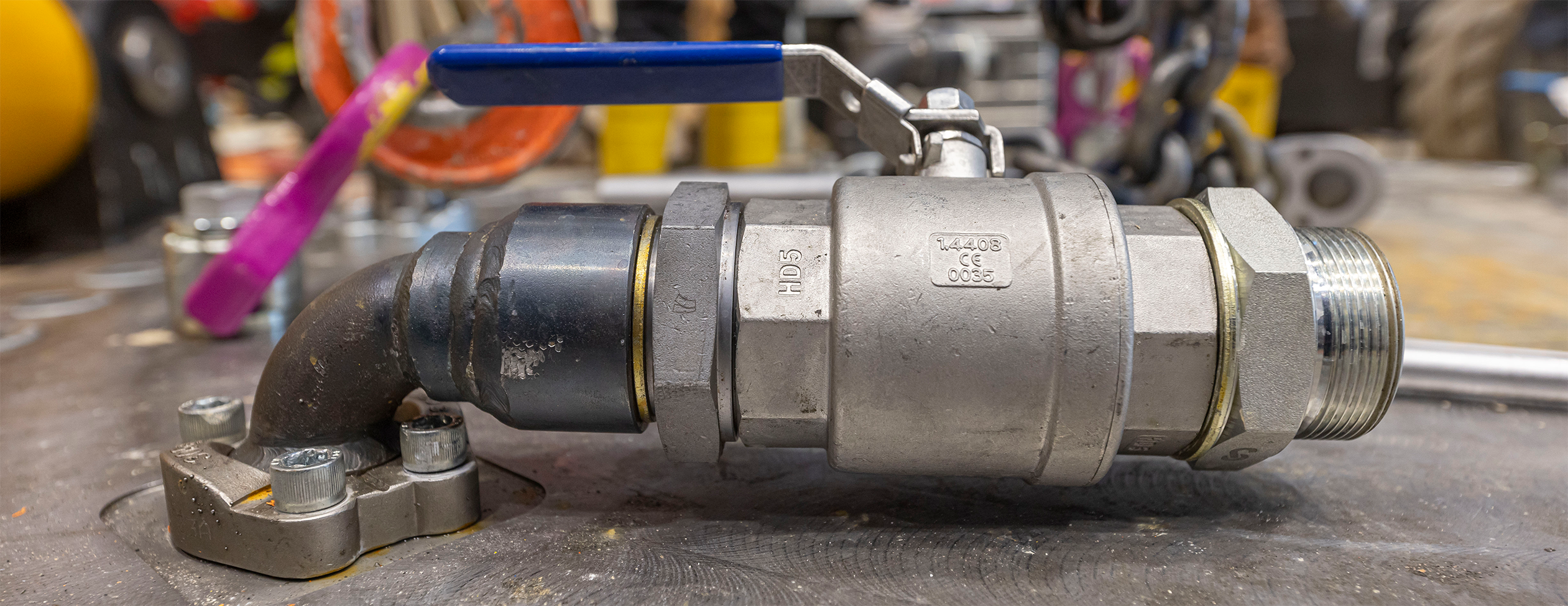
To build up the pressure, we need two pumps. The small pump is used to inject water into the monopile up to the point where the water flows out.
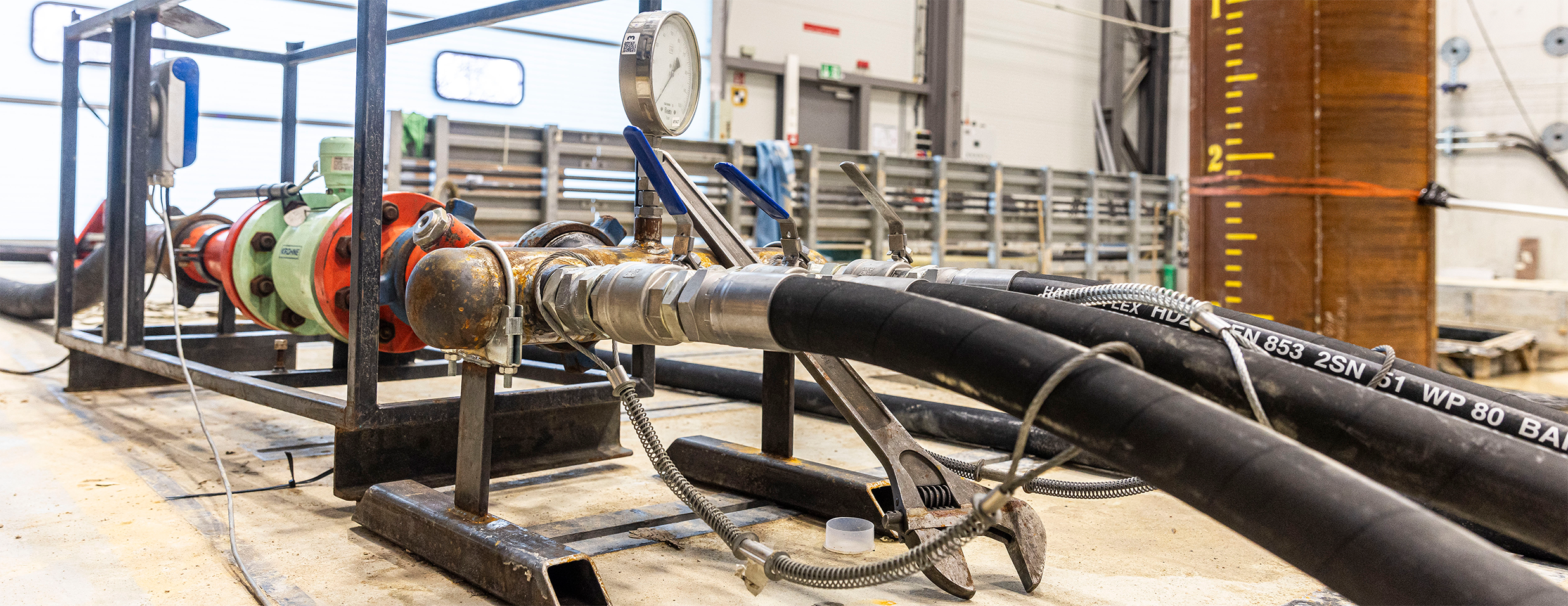
And as soon as the monopile is filled with water, we turn on the BIG PUMP. This allows for much larger flows and much higher pressures. That is the pump that we use for the hydraulic extraction process.
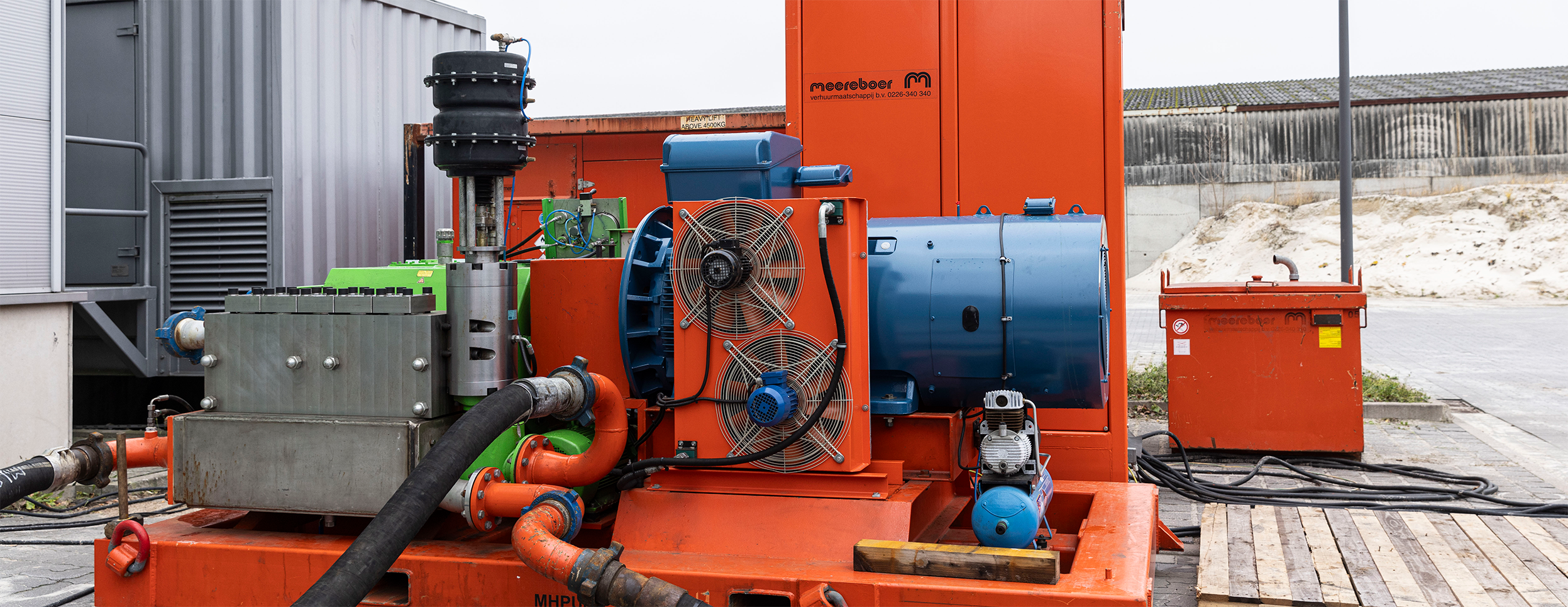
…and lots of water. For this project, these water containers were used to store the water used during the tests. Fortunately, at sea, you would not need these water containers. We would use seawater.
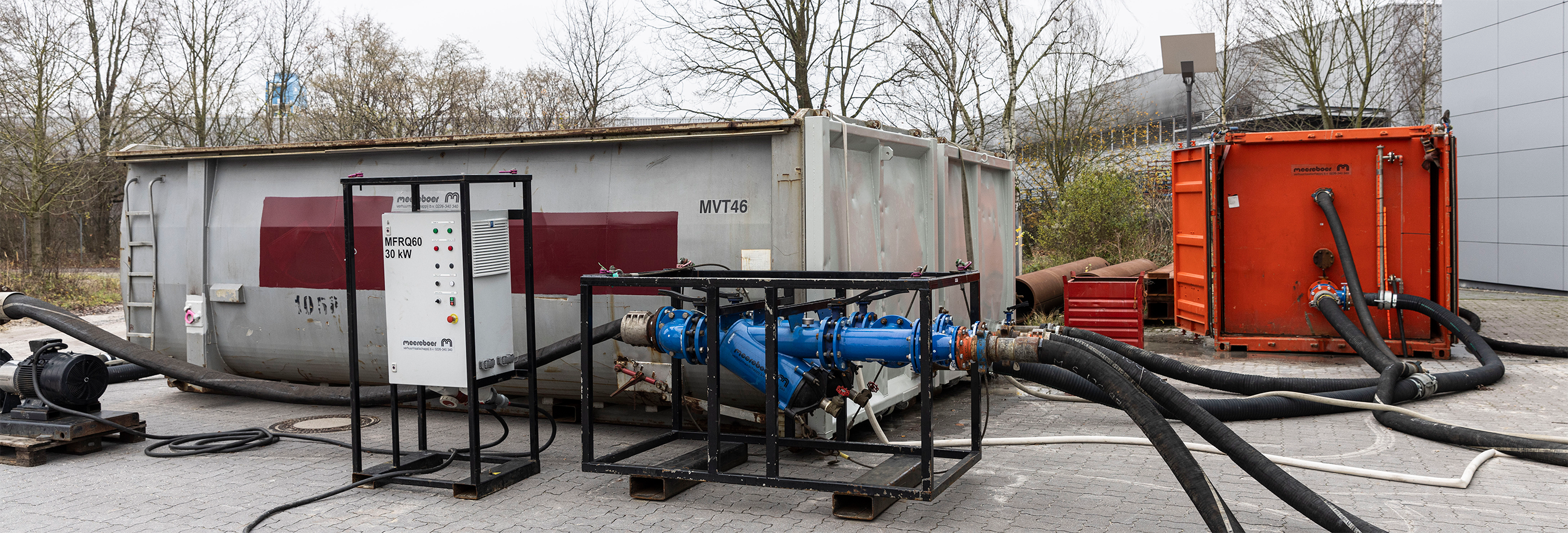
The underwater noise levels are much lower than with the current methods. The noisiest part is the noise generated by the pumps and the generators, and a little bit of the water hitting the lid. However, this is all above the seawater level – on the vessel and at the tip of the monopile –, so this will not produce much underwater noise. It is not much noisier than a truck driving in front of your house. So, this is good news for marine life.
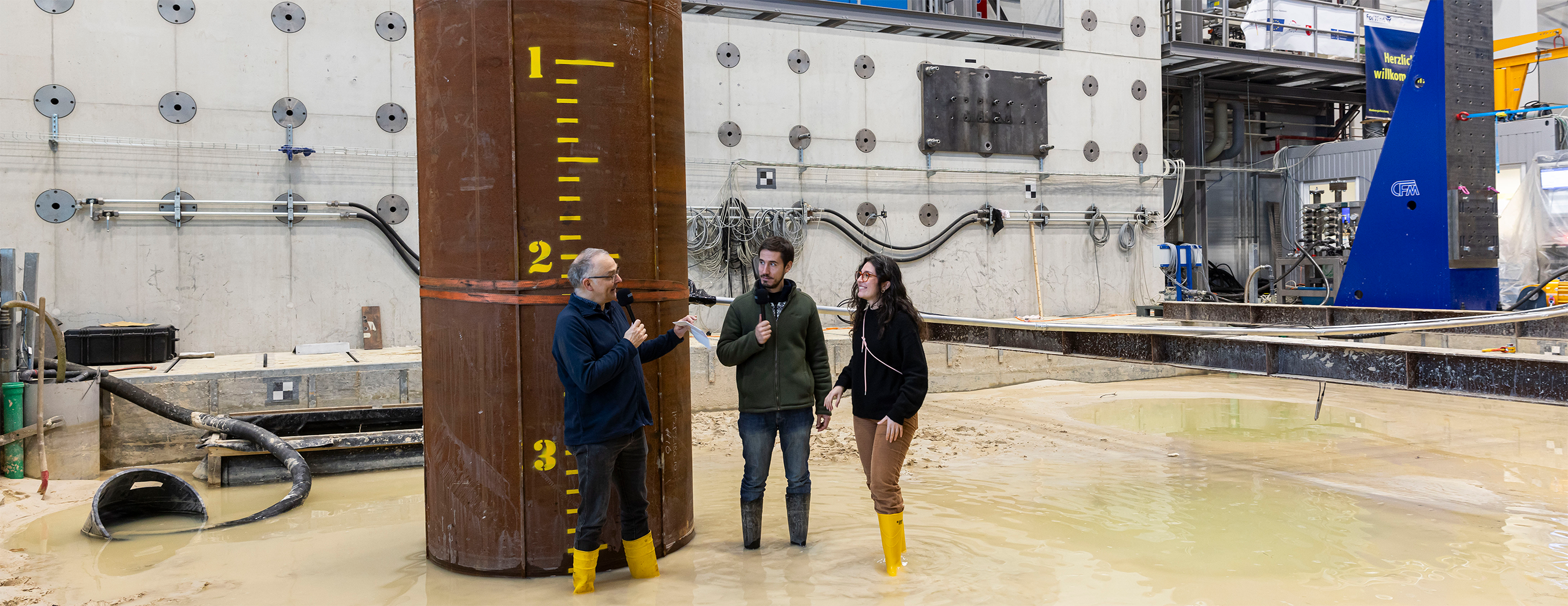
Sensors
Alba: “During these tests, several sensors are installed. The data we gather from these sensors will be used to improve the models and understand what is happening inside the pile. However, in reality, during the decommissioning of an offshore monopile, you don't need these sensors. You would only need one sensor under the lid to monitor the pressure; that should be sufficient to control the process.
In the first pile, we had fibre optics along the pile wall to monitor the strain and deformation of the pile during the process. Because the wall of the monopile must withstand the high pressure that builds up in the pile. It is looking good so far, and we did not visually see any obvious deformations. Analysis still has to be done.”

Better together
“RWE initiated HyPE-ST 1 in 2019, but we also have many companies that are partners in this project. IQIP, RWE, DOT, Deltares, Sif, TNO, Jan de Nul, KCI are involved in the tests and TNO is leading the development of the numerical model. Having all these partners with their specialised knowledge was very important because in this way we ensured we didn't overlook any important aspects,” said Anderson.
IQIP: Expertise in installation equipment
Jan de Nul: expertise in installation
KCI: engineering company part of the Sif group
RWE: expertise in project development and operating wind farms
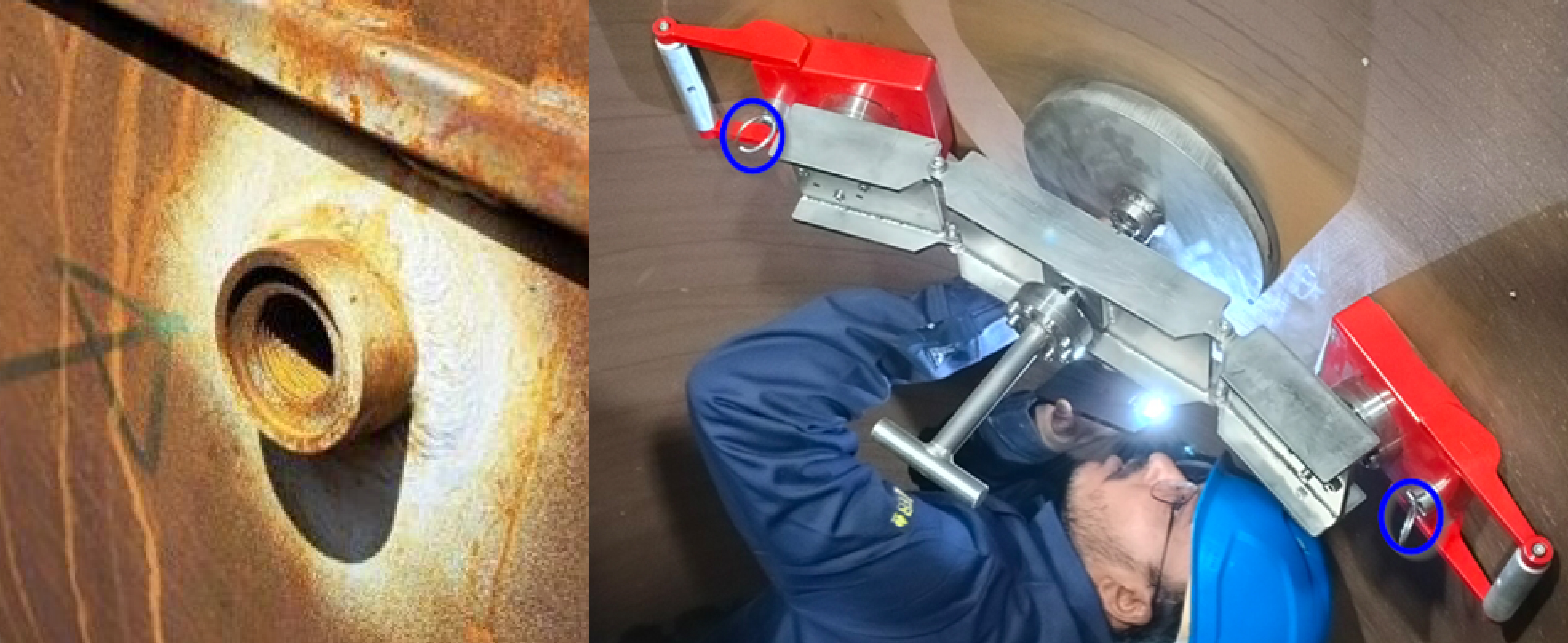
One example of these aspects is that offshore monopiles have holes in them. These are to let the cables come out of the wind turbine to be connected to the network. But… with a hole in the pile, you cannot build up the pressure. Anderson: “KCI, part of Sif, designed a hole-closing tool. This was placed inside the monopile with a high-power magnet to hold in place and ensuring the hole is closed so the water cannot go out. That was also another exciting part of the second test.”
Sif: expertise in monopile manufacturing
TNO: expertise in applied research on modelling and novel measurement techniques
Find out more about the HyPE-ST 1.2 project.
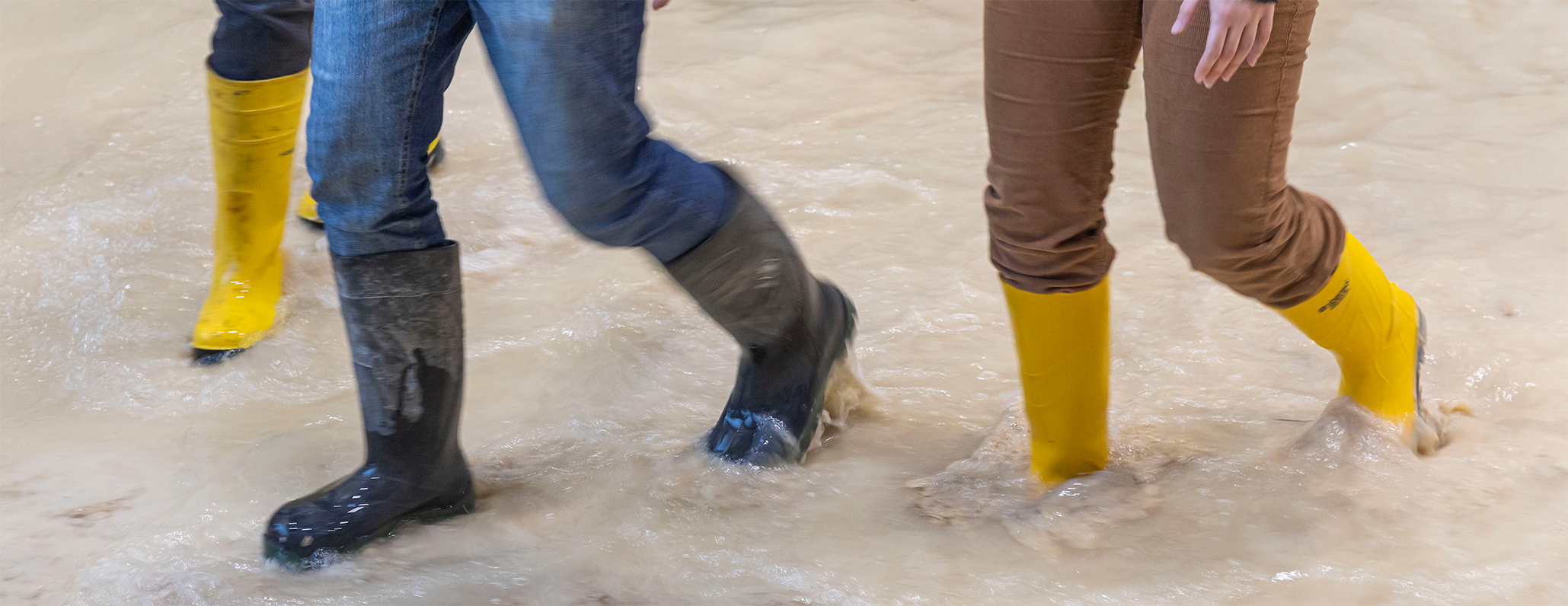
© GROW ’25