Getting to the bottom of things
It sounds like a beautiful beach day: playing around with water and sand in an environment that cannot be taunted by rain. But doing so can result in more than just sandcastles.
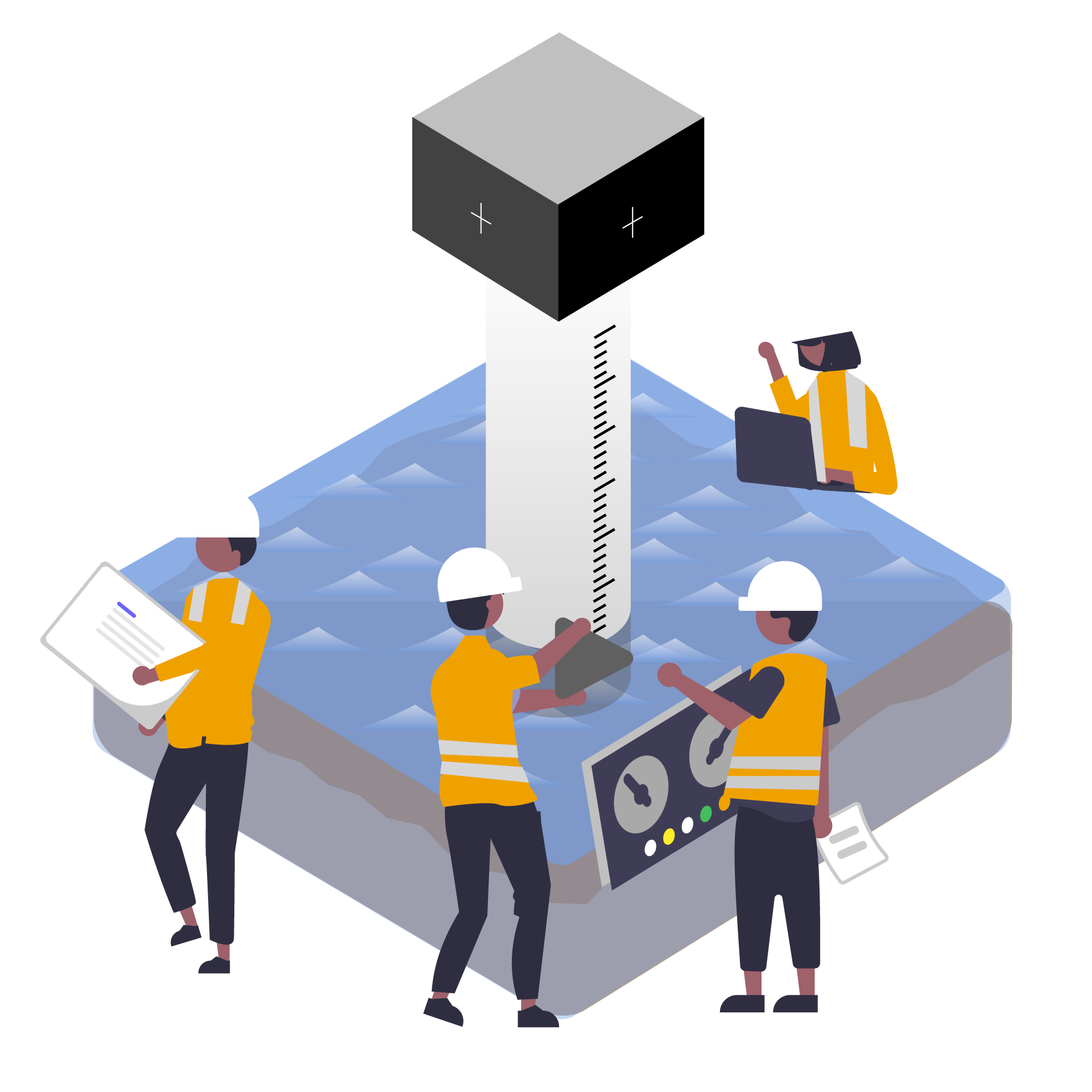
As the size of offshore wind turbines increases, monopiles get bigger as well. New installation technologies are currently being investigated, further developed, and tested in the SIMOX (Sustainable Installation of XXL Monopiles) R&D project. The aim is to enable the installation (and decommissioning) of future XXL monopiles in the North Sea sands. And all of this in a sustainable, cost-effective, societally, and environmentally acceptable manner.
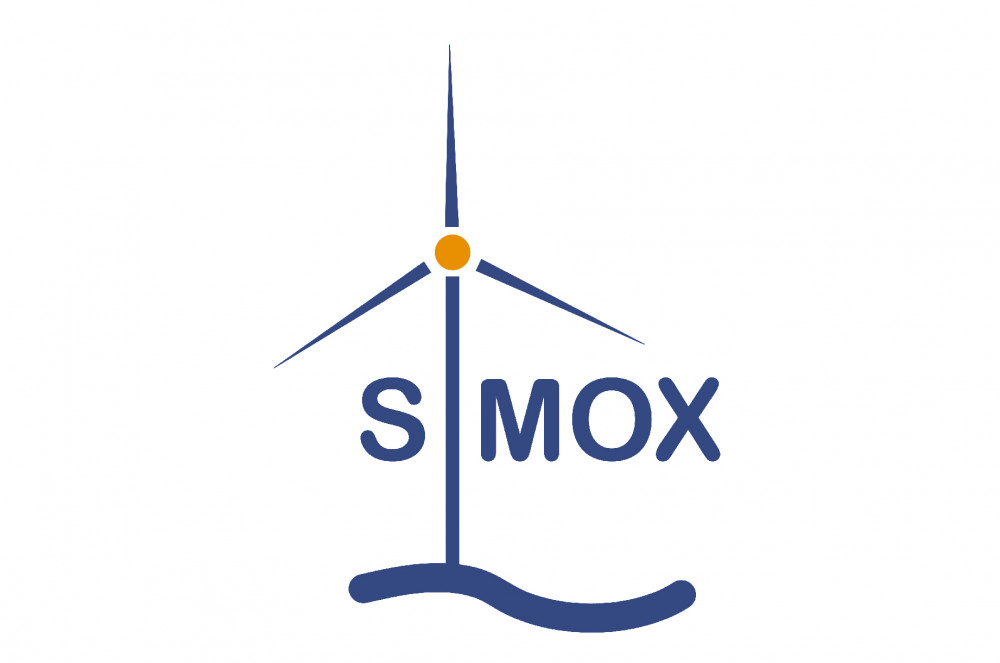
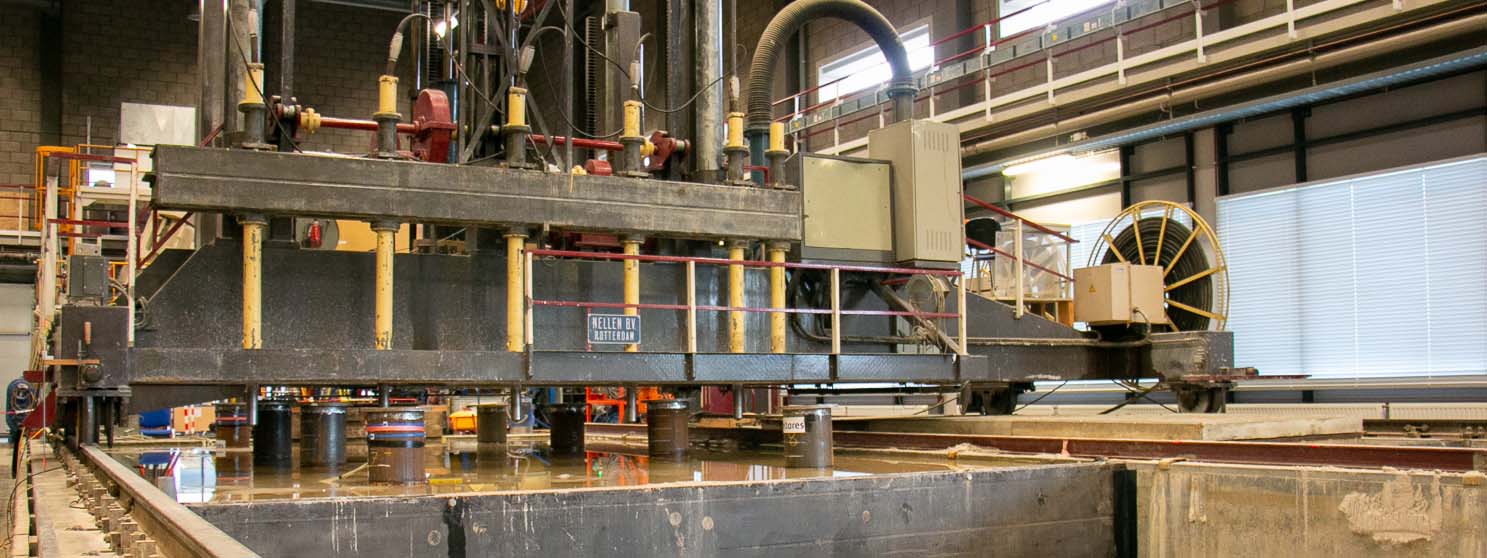
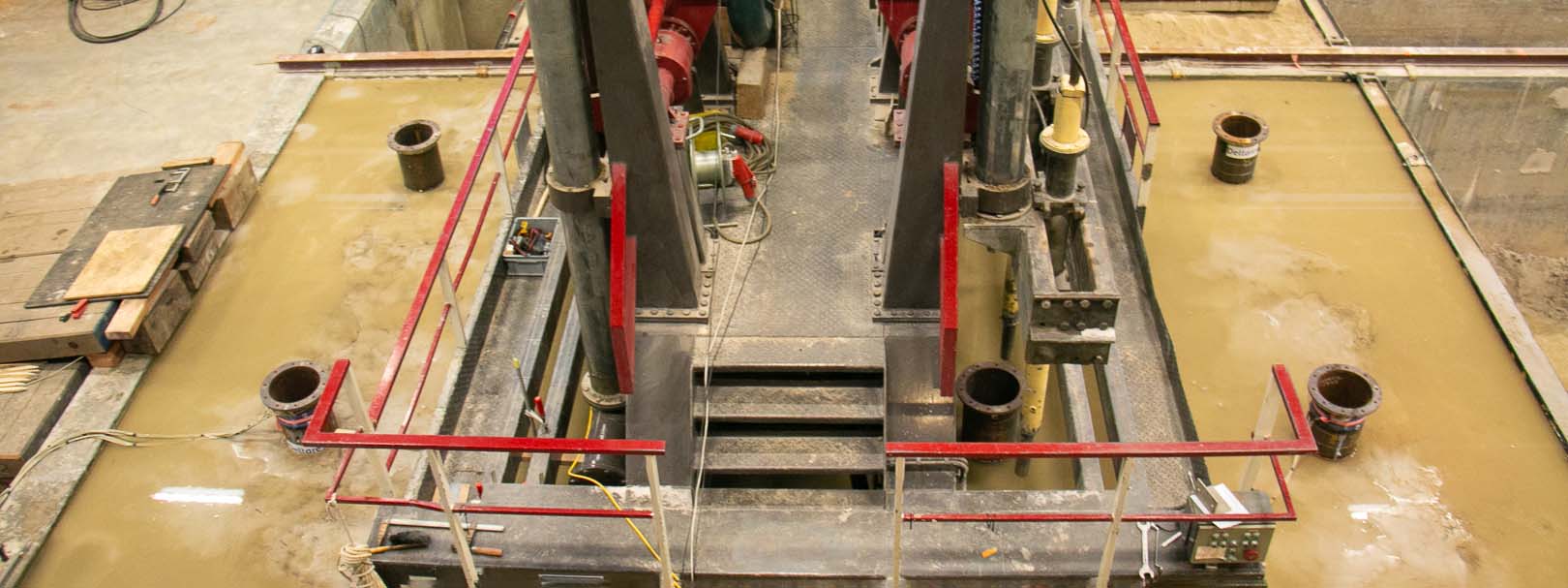
Bigger piles, but not bigger hammers
Currently, the most widely used method of driving monopiles into the seabed is hydraulic impact pile driving. So why do we need new technologies? Why not use bigger hammers to get these bigger piles into the ground? Mark is the first to admit that hammers are not being dismissed, but he also explains: “I think we will continue to use bigger hammers. However, with hammering, additional noise mitigation measures to protect the environment are needed; this is costly and time-consuming. So instead, the Dutch have been innovating, and the new techniques involved in this project aim to reduce noise generation and possibly make noise mitigation redundant.”
Several candidates
The first technique is vertical vibration. This means moving the pile up and down to drive it into the soil. It’s an old and successful technique for onshore projects. However: “It has not been certified for use in offshore projects yet,” according to Ahmed.
Have a look at Ahmed's profile on LinkedIn

The second technique is called Gentle Driving of Piles (GDP). “What happens in GDP is that you combine a high-frequency torsional vibration (in the horizontal plane) with an axial vibration at a lower frequency. Both motions can be decoupled and have their own amplitude. Previous projects have shown that GDP could be a very promising technology.”
Have a look at the project pages of Gentle Driving of Piles and Gentle Driving of Piles 1.2
Or listen to and read the GROW-to-GO edition about GDP.
A third technique can support the first two technologies and also conventional impact hammering. The Vibrojet® is a combination of a vertical vibro hammer and jetting near the pile toe. This fluidises the soil inside the monopile, which helps the monopile to go into the ground more swiftly.
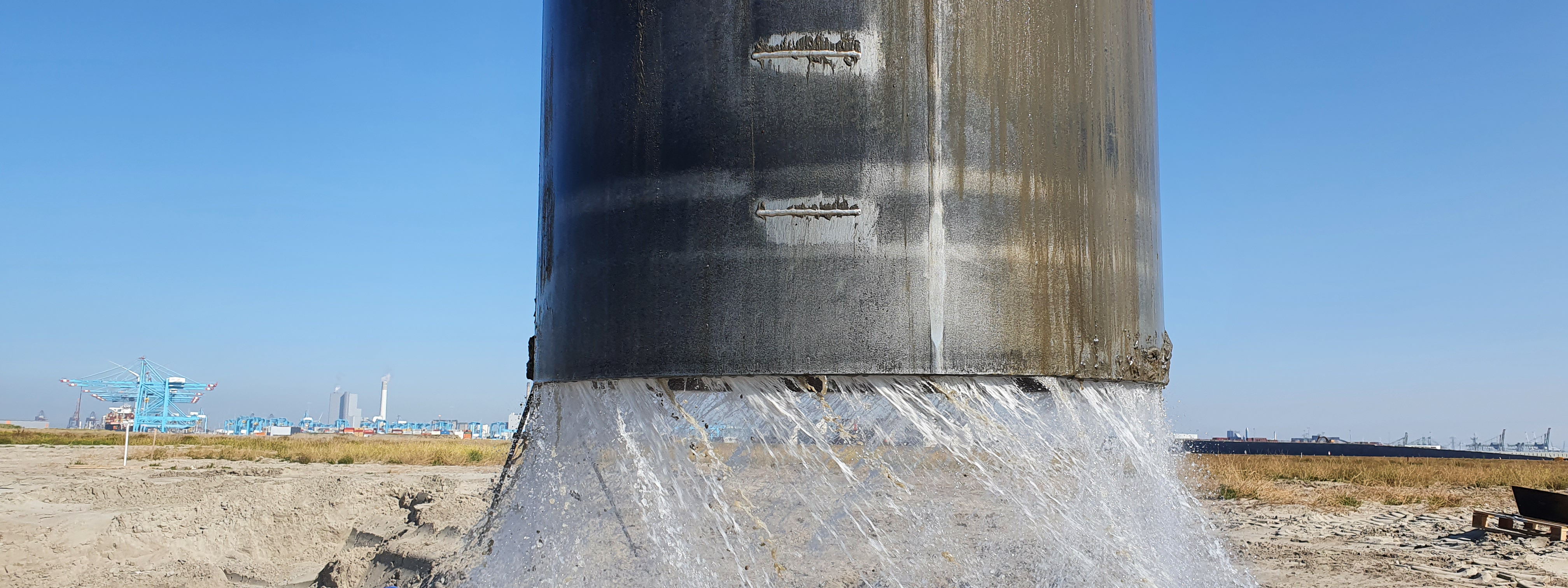
In SIMOX, these technologies are being compared in the laboratory and onshore tests, resulting in a better understanding of their behaviour and performance under similar conditions.
"We don't know which technique ends up being most successful offshore." Ahmed says: "It is very well possible that different techniques will be used in different conditions. But, whatever happens, all techniques will help save costs, and time, and be more environmentally friendly."
Boskalis: expertise in installation
Cape Holland: expertise in installation of equipment
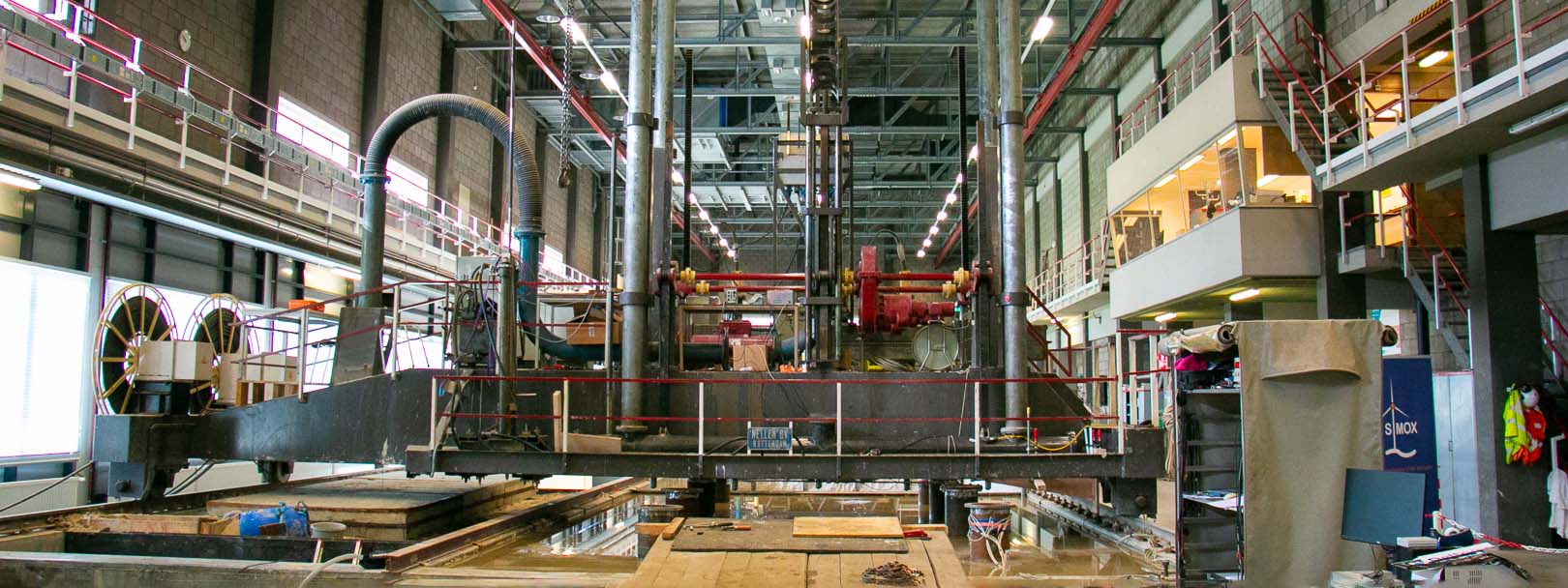
Drivability
Standing in the Water Soil Flume at Deltares, a big hall with a big tank, water and sand, we witness tests with eight scaled steel piles that have been driven into the soil using different techniques. For the tests, the piles were equipped with sensors. Thanks to these, the speed and stresses on the piles are recorded during the driving. This can help understand the “drivability” of the piles into the soil. After the installation, the piles are cyclically loaded in the horizontal plane, a thousand times per monopile, to see what happens with the piles interacting with the ground. This simulates the forces of waves, currents and wind on the structure.
Deltares: expertise in geotechnical research
DOT: expertise in wind turbines
GBM Works: expertise in installation equipment
Heerema Marine Contractors and Heerema Engineering Solutions: expertise in installation
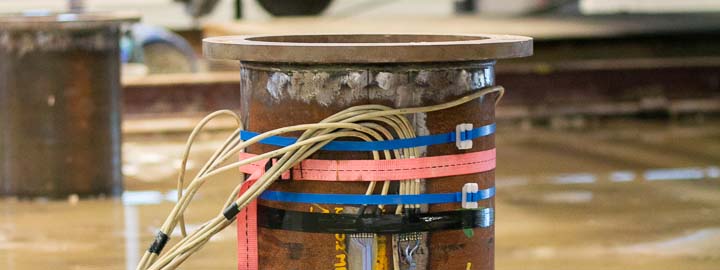
Size matters?
So, will this small-scale experiment be representative for the real-life piles at sea? Mark admits that “there is quite a difference between these piles and the real ones. What we hope to do here is to see trends and get a feeling of how the piles and the soil behave. And with the knowledge we gain here, we think we can better prepare for the onshore tests that will be executed with larger-scale piles.”
IQIP: Expertise in installation equipment
Ocean Winds: Expertise in project development and operating wind farms
Ørsted: expertise in project development and operating wind farms
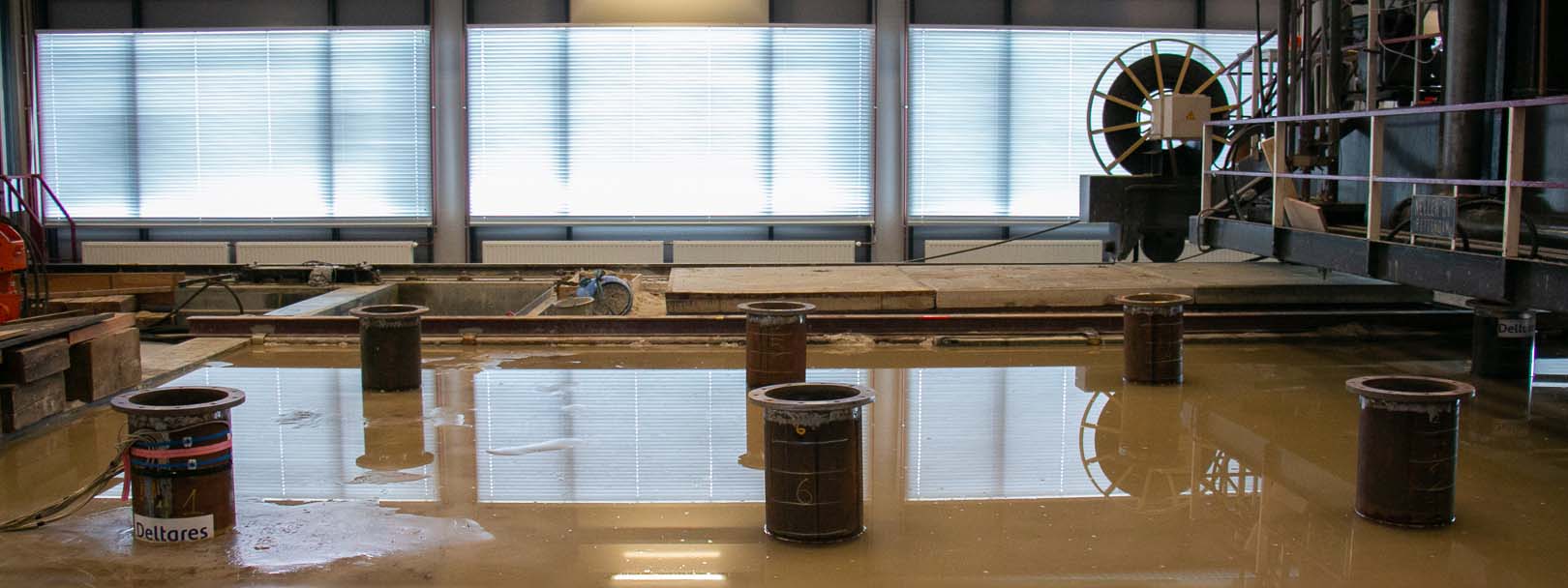
These tests will result in high-quality experimental data sets and validated pile-driving & lateral-bearing capacity models. A new element will be the refusal depth prediction in medium-dense and dense sands, which could be extended to stiff clay and layered soils.
Furthermore, noise prediction models that are able to predict noise levels and frequencies up to 750 m from the source will be further developed. And we will assess the noise reduction potential for the different technologies and guidance in this area for regulators.
RWE: expertise in project development and operating wind farms
Seaway 7: expertise in installation
Shell: expertise in project development and operating wind farms
Siemens Gamesa: Expertise in wind turbines
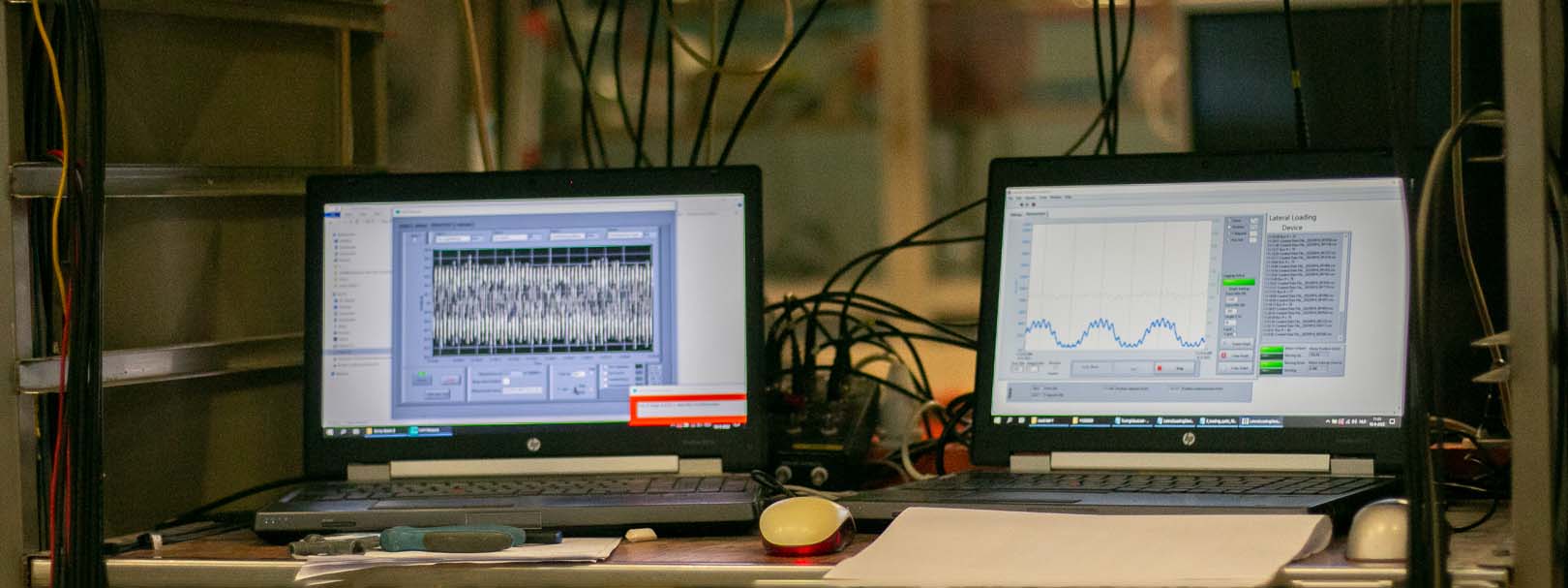
The project also aims for high-quality testing data sets and models for predicting the lateral bearing capacity of piles. And last but not least, the project explores the suitability of these technologies to extract the monopiles at the end of their lifetime.
So it's not just this lab test that will deliver insights; it's the combination of tests that will provide the answers that the industry is looking for."
Sif: expertise in monopiles
TNO: expertise in applied research on novel measurement techniques
TotalEnergies: expertise in project development and operating wind farms
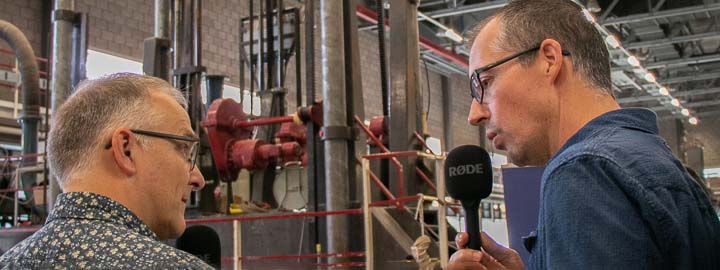
Industry interest in innovation
Even though some partners are competitors of one another, they work together by exchanging knowledge and experience. In this way, this project differentiates from others – Ahmed admits to never having seen a Joint Industry Project where “the industry is so much engaged and actually wants to participate in the research, to think along and is eager to implement the outcomes in full-scale projects. And especially by combining the knowledge of all the partners representing the supply chain, we can get insights we cannot achieve individually.”
TU Delft: expertise in structural (dynamics) research
Van Oord: expertise in installation
Vattenfall: Design and maintenance of offshore wind farm
Find out more about the SIMOX
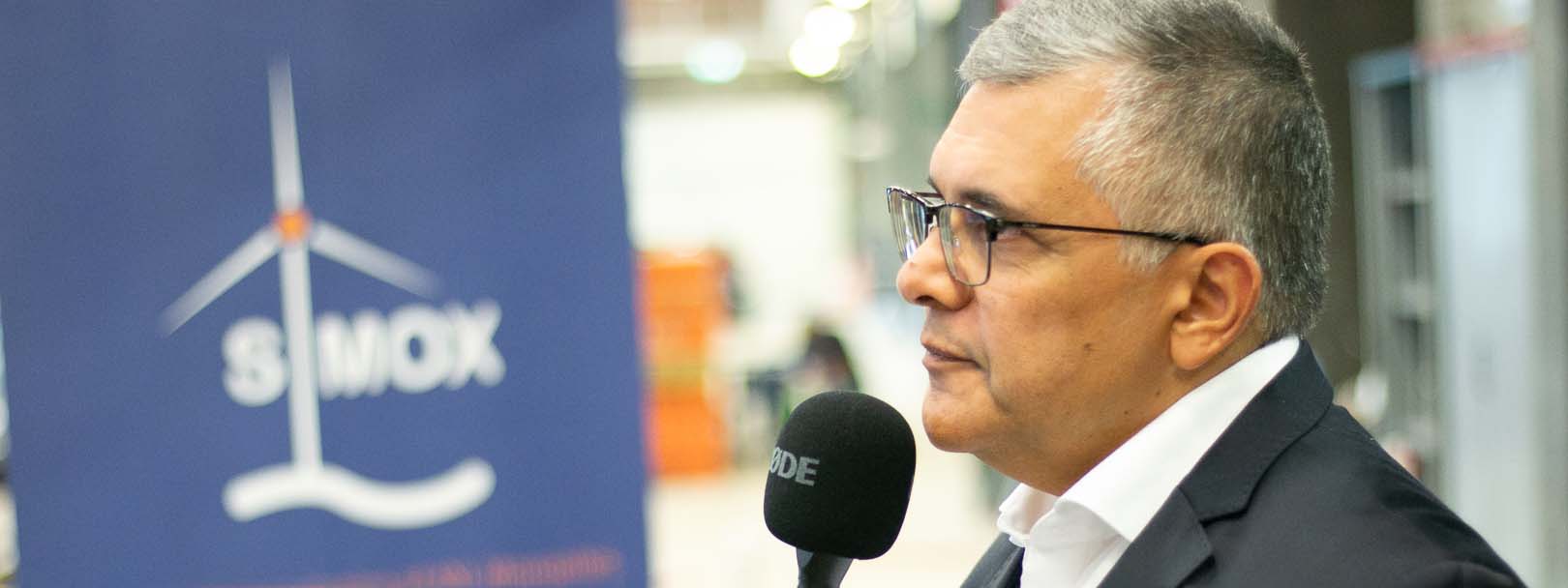
© GROW ’25