On the rocks
Rocks barely sound interesting, yet they are essential for the stability of wind turbine foundations. After all, they are used to prevent the erosion of sand around the monopile. Currently, the installation process of the scour protection requires three steps. Therefore, the Optimising Pile Installation through Scour protection (OPIS) project is researching how to improve this process. The research is well underway, and its researchers are nothing but “optimistic”.
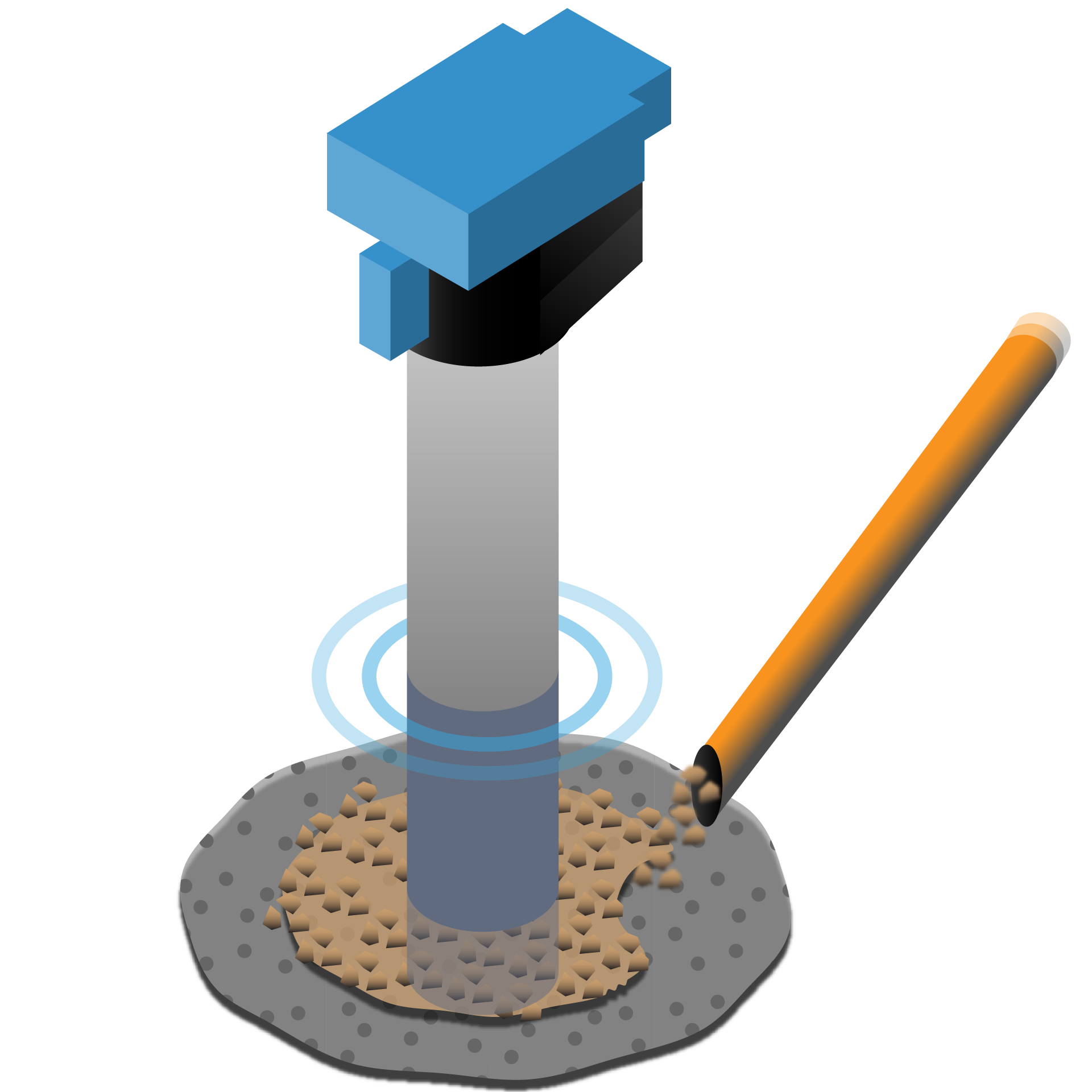
“Scour”?
Have a look at Ton's profile on LinkedIn
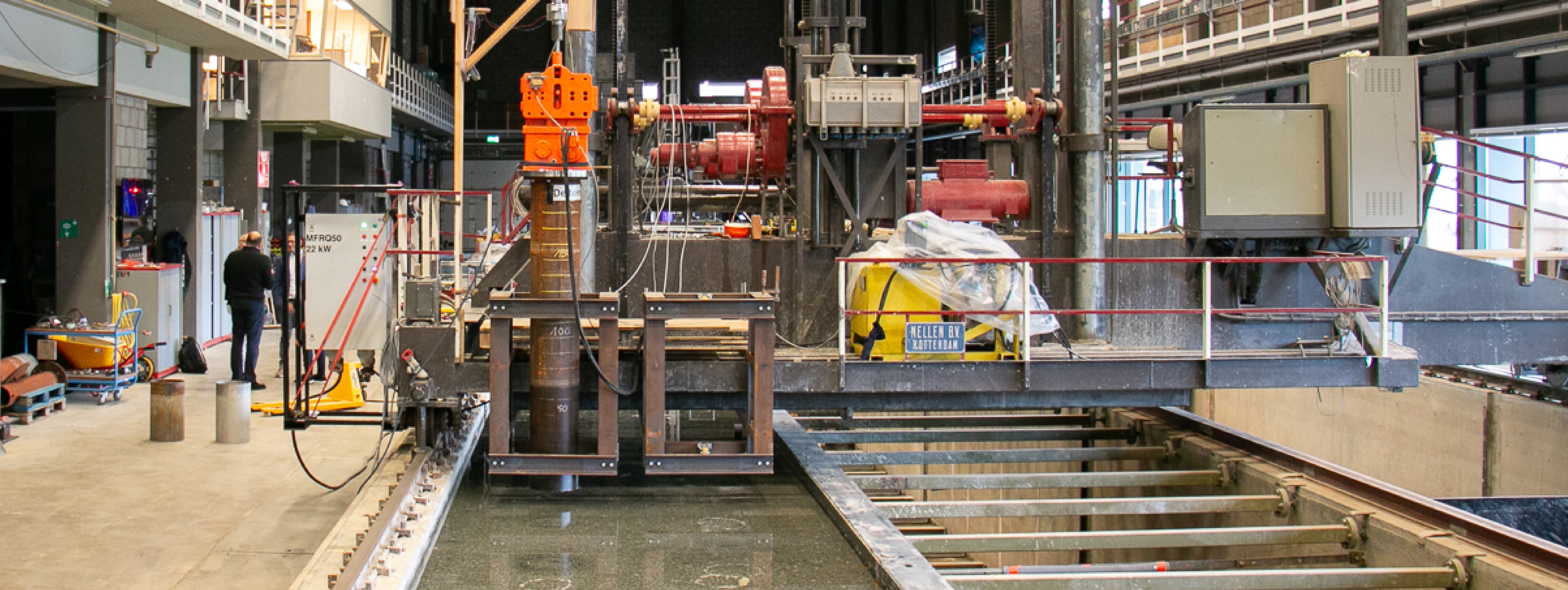
The OPIS team believes this procedure can be optimised: “Well, let’s do it in one go. Install the piles through both layers in one go, and you only need one ship,” Ton enthusiastically says. Easier said than done…
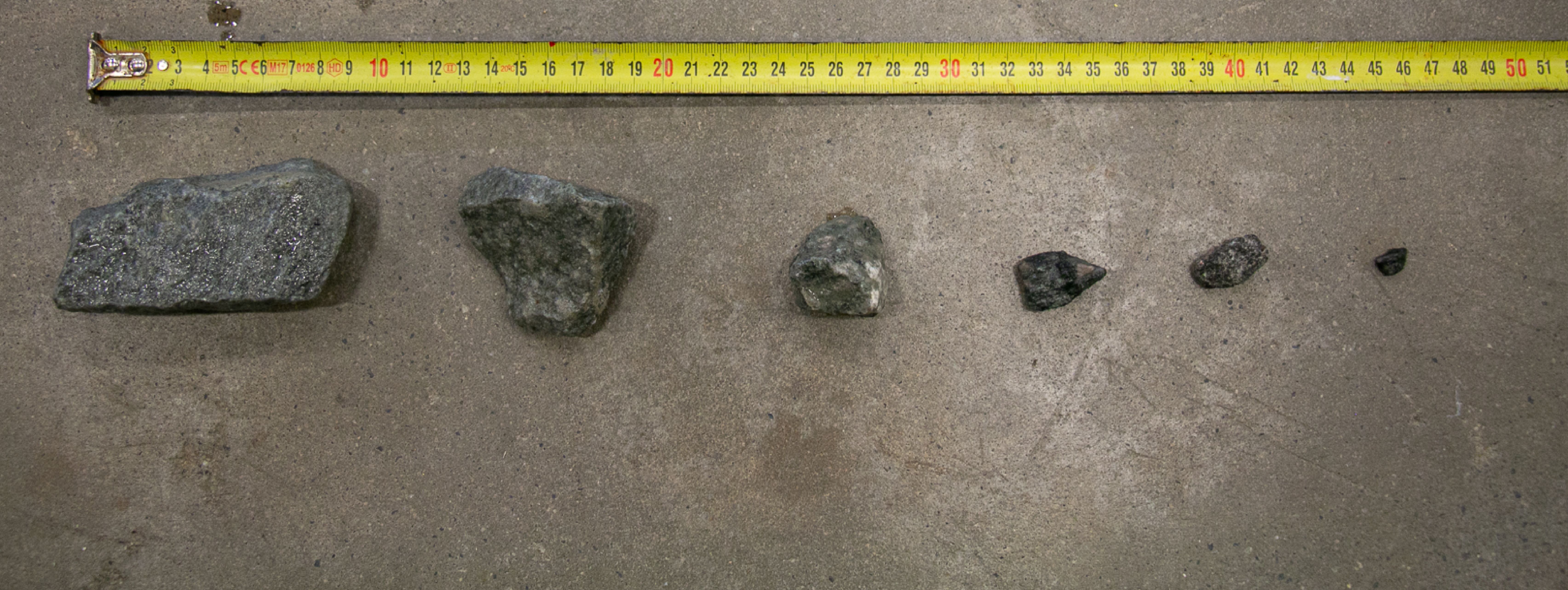
Challenges
Like anything, the plan has its challenges. So, we want to get a better understanding of the physics behind the behaviour of the pile, rocks and soil during installation. Ton says: “We want to ensure this option works. Will the pile get through the scour layer by its own weight, noting that the mass of a pile can be above 1000 tonnes and, in the future, even 4000 tonnes? And we want to know how much extra force from a vibro- or impact hammer tool will be needed?” The integrity of the pile is also tested to ensure the rocks do not damage the pile or its coating. The researchers also look at the displacement of the rocks and the soil.
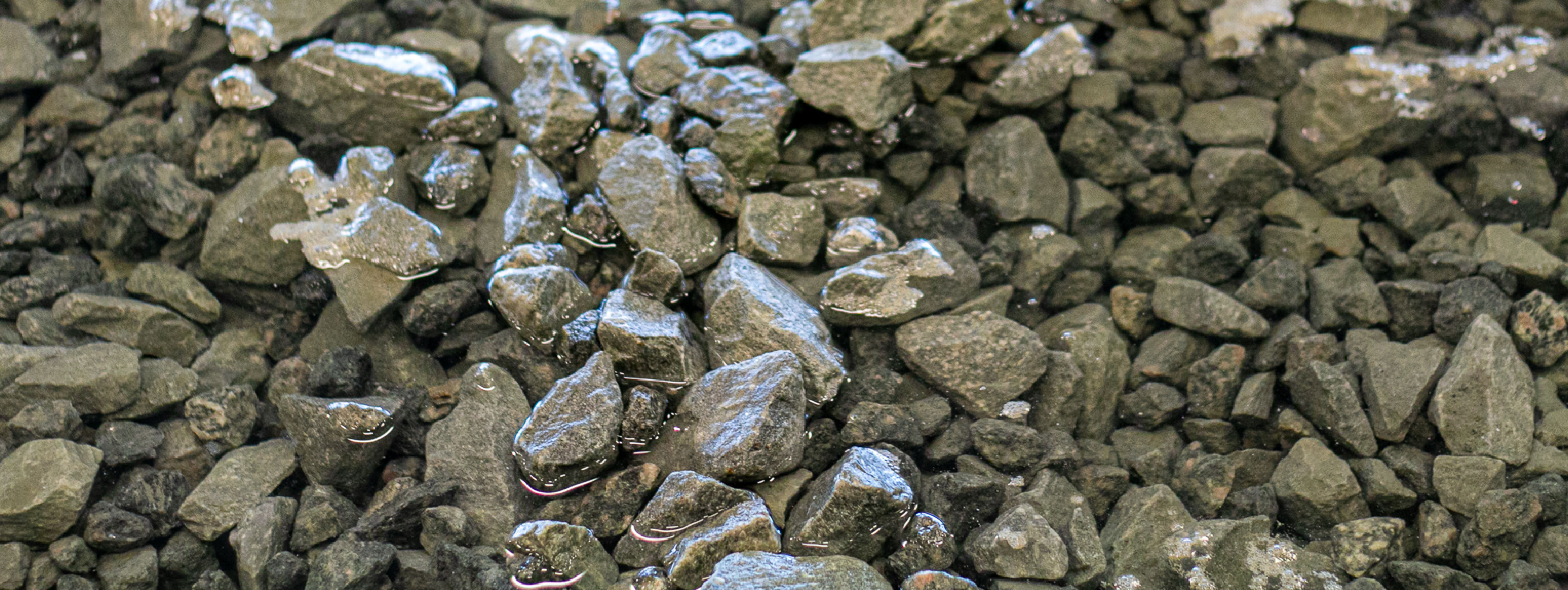
So let’s test!
Have a look at Cihan's profile on LinkedIn
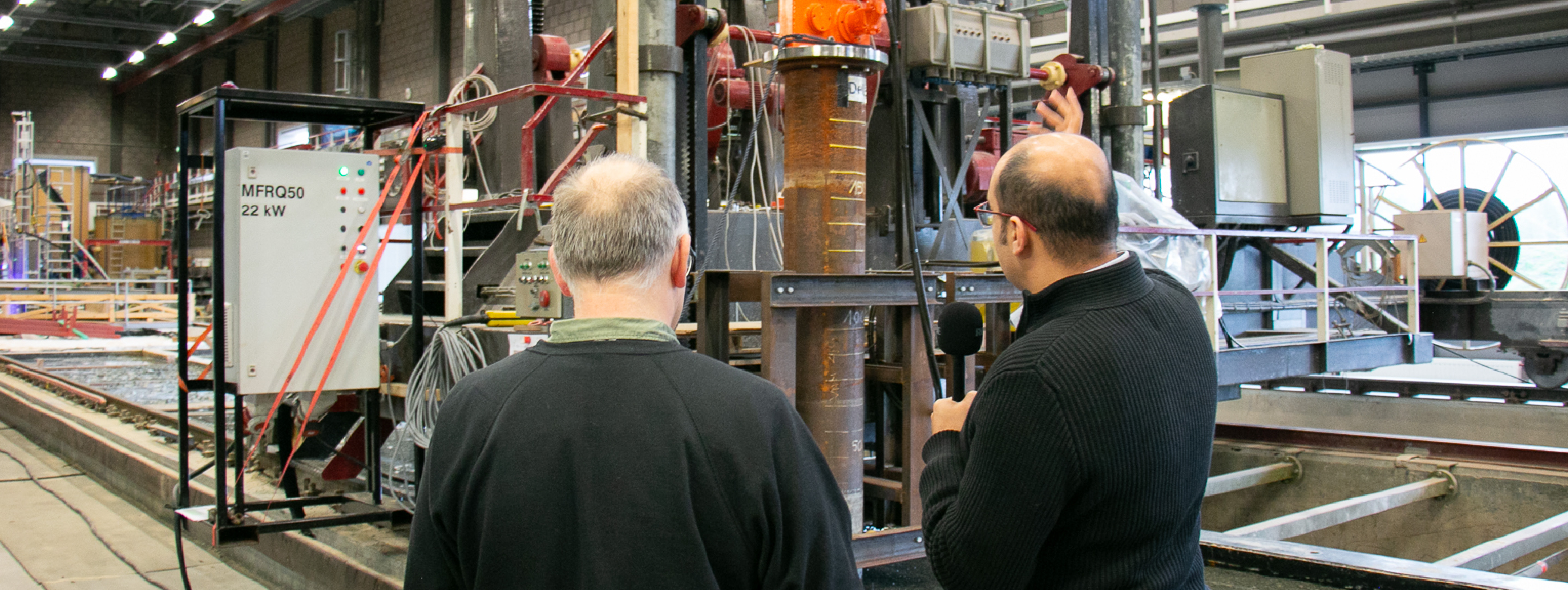
We will let the pile touch down on the rock layer. We will ensure that it buries itself into the rock under its self-weight. We have carefully engineered it so that it won’t go through all the rock layers we have. And then Marcel Busink (technician) turns on the vibro hammer to let the pile penetrate the rock entirely into the model seabed.” Sensors all around are precisely calibrated to capture and measure every change.
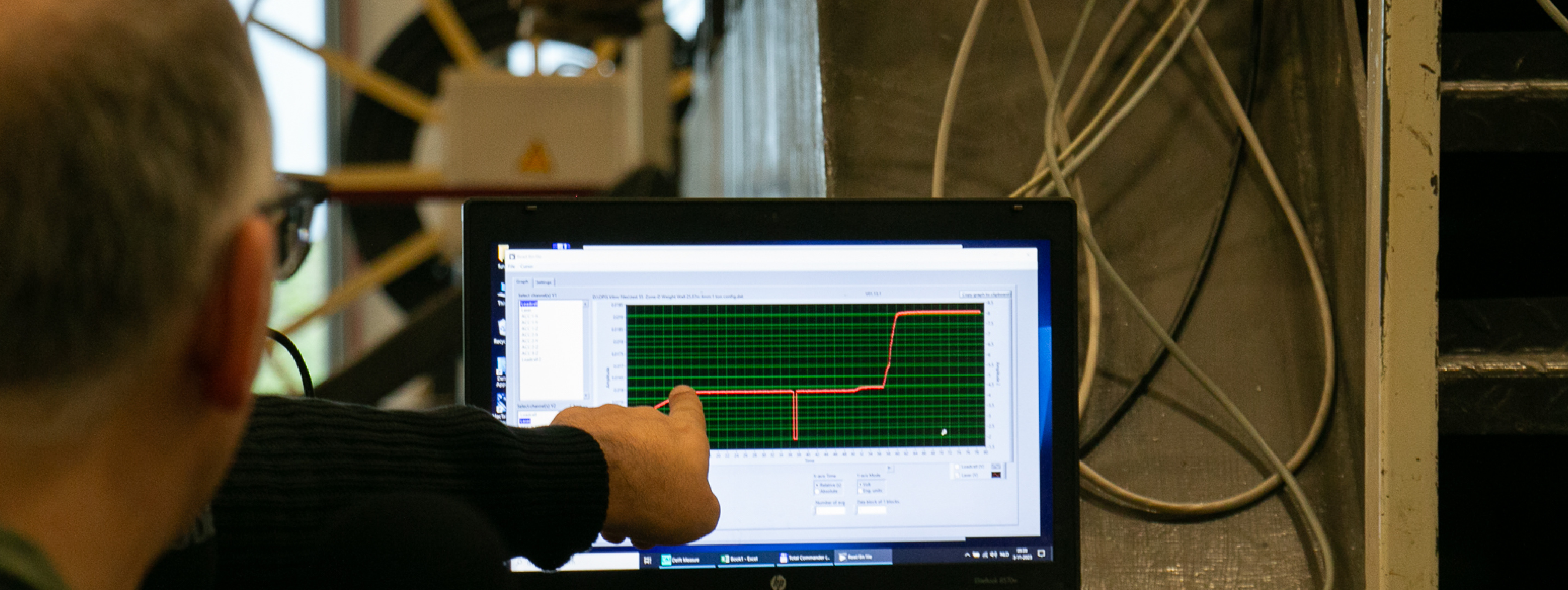
The benefits
Reducing the installation time of wind turbine foundations will have significant advantages. First of all, for a wind farm of one gigawatt, the estimated cost savings are in the order of 3 million euros. The process will also reduce the carbon footprint of the whole process.
CAPE Holland: expertise in pile installation equipment
Deltares: expertise in geotechnical engineering and scouring
DEME Offshore: expertise in offshore pile foundation installation
Equinor: expertise in project development and operating wind farms
Heerema Engineering Solutions: expertise in engineering solutions for offshore challenges
Heerema Marine Contractors: expertise in offshore pile foundation installation
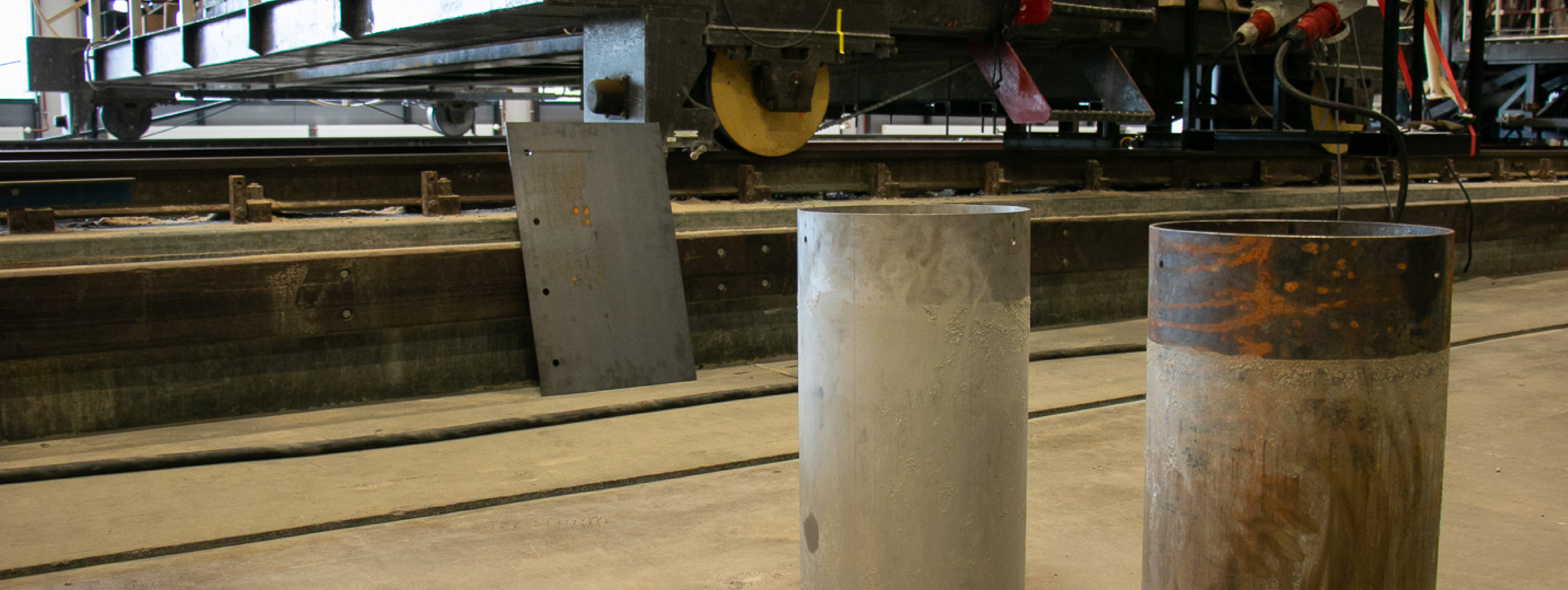
The current dataset is already valuable to the industry and will be further extended during the rest of the project, which is scheduled to be finished at the end of 2024. That is, without any more disappointments that keep Ton up at night. “We anticipated using a test facility in Hannover, Germany, but that facility is booked until 2025. That was stressful. However, I am convinced we will find another test facility in time .”
Jan de Nul: expertise in offshore pile foundation installation
Seaway 7: expertise in offshore pile foundation installation
TU Delft: expertise in modelling behaviour of granular materials
Vattenfall: expertise in project development and operating wind farms
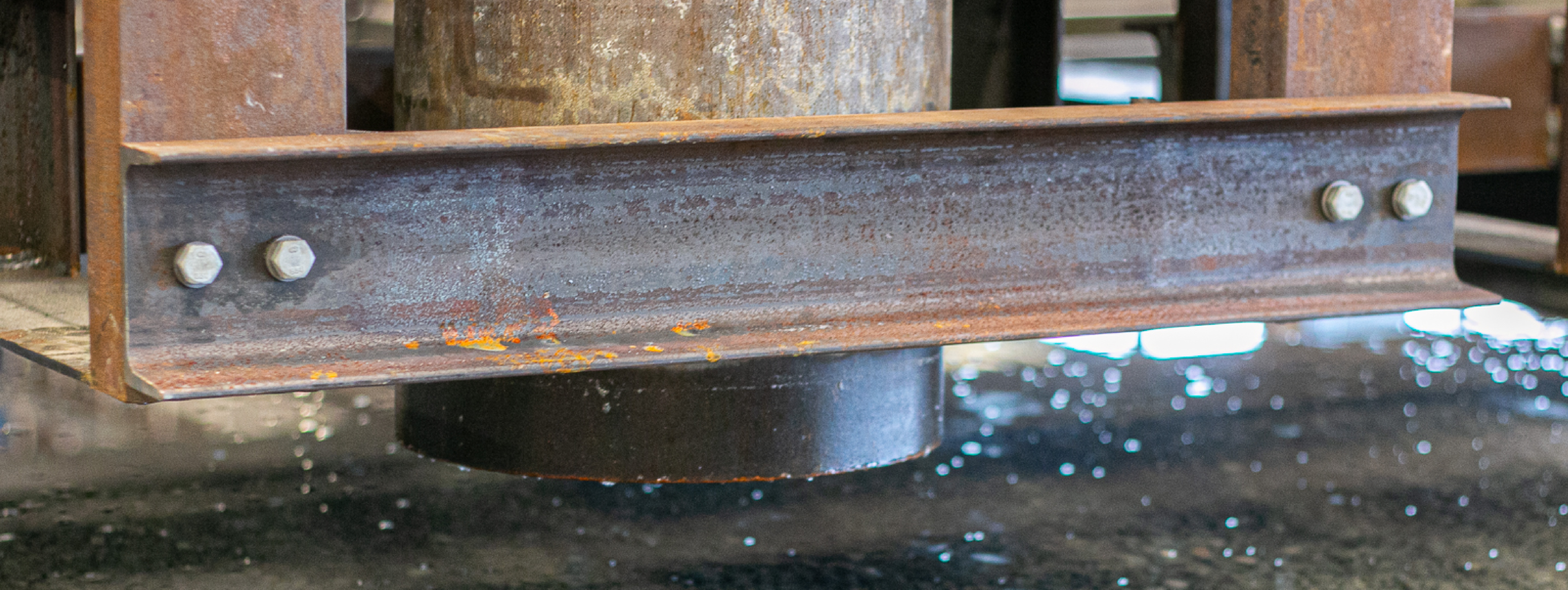
Good perspectives
Ton and Cihan agree that everything is looking good. “It’s a very promising approach, and we’re sure it’ll work. But we must be absolutely sure before we roll it all out.” With all the data we gathered, we can improve our understanding, and hopefully, the new installation approach will be ready by 2025 to be implemented.
Find out more about the OPIS project
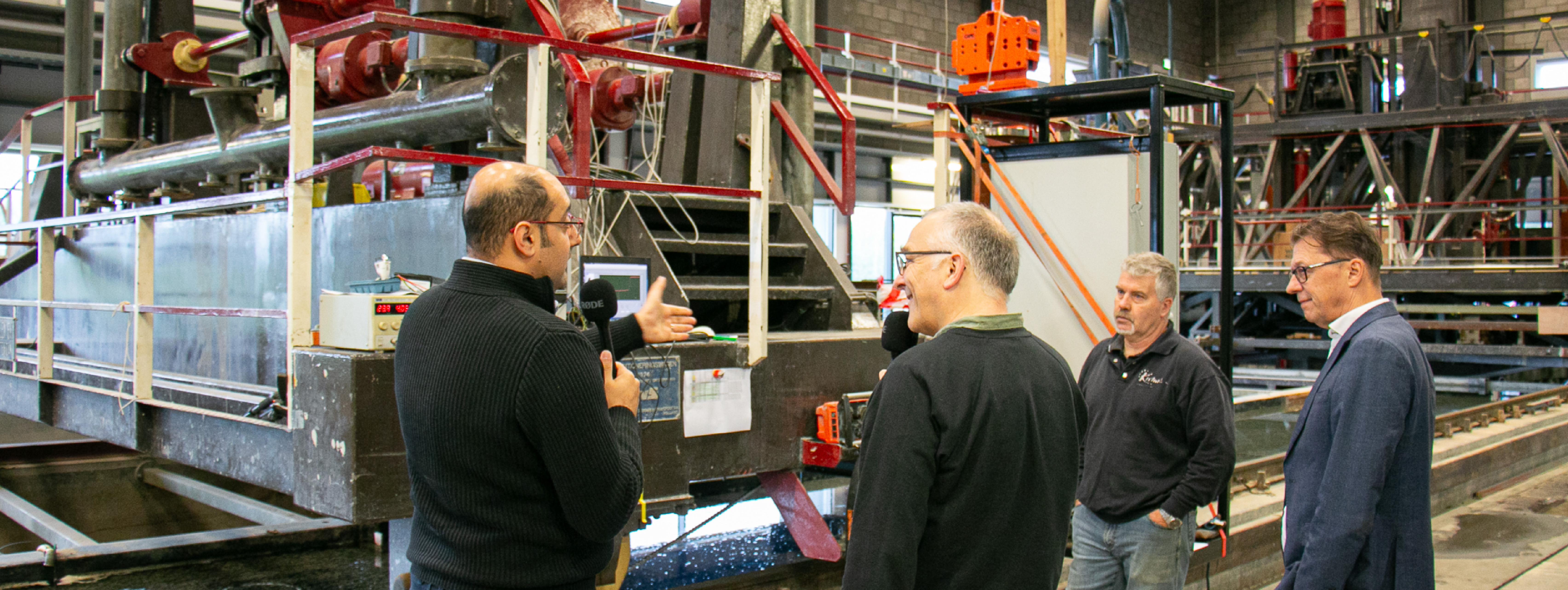
© GROW ’25